In today’s competitive and fast-paced world of supply chain management, cross-docking is a process that helps companies achieve new efficiencies and match customer expectations. By reducing the need for material handling and storage wherever possible at different points in your supply chain, you can reduce warehouse waste and free up capital at the same time.
For a high-level overview of what cross is, watch this short clip from our new podcast.
There may be many reasons why your company is considering cross-docking in your organization, but there are benefits and risks to keep in mind. In this post, you’ll find out how cross-docking works, what are the main examples of cross-docking, and how cross-docking can reduce costs.
Quick Takeaways:
- Cross-docking helps organizations to add new efficiencies to inbound and outbound logistics
- Instead of warehousing goods and managing shipments on a regular schedule, cross-docking emphasizes the need to keep goods flowing
- With more organizations now dealing with ecommerce and B2C operating models, cross-docking is becoming the popular way to maintain supply chains
What is Cross Docking?
Cross-docking is the process of planning and managing the distribution of products by removing the storage portion from most of your supply chain management process. Instead of warehousing products at intermediate stages of the journey, cross-docking allows you to sort and reload items directly onto outbound vehicles for a leaner, more agile supply chain.
Depending on your current supply chain strategy, you can cross-dock large shipments into smaller groups, or use cross-docking purely for your last-mile fulfillment tasks. With the latest advances in technologies, more organizations now opt for a cross-dock warehouse instead of depending on strategically placed, geographically separated depots.
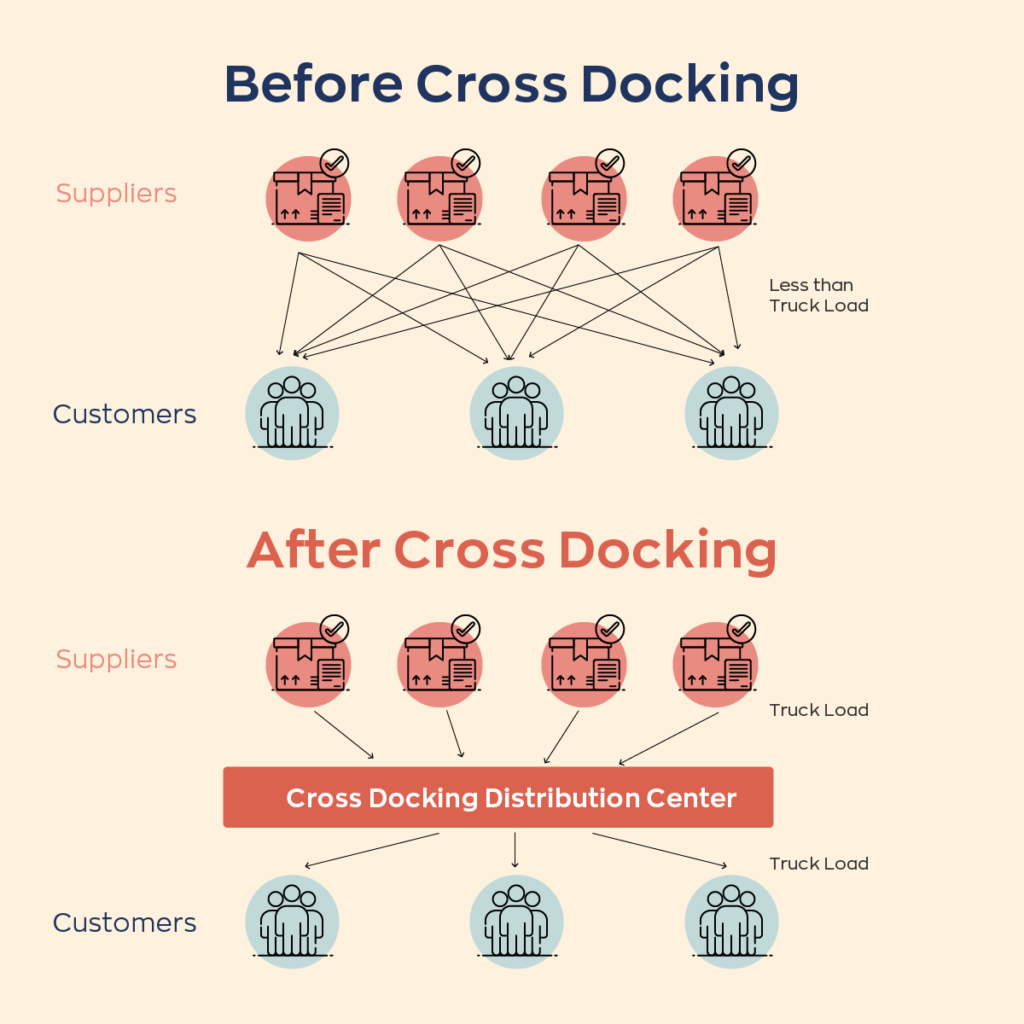
Examples of Companies Using Cross Docking
Depending on the size of the business, cross-docking approaches can range from relatively simple to highly complex process management. Using a range of digital and physical technologies makes it possible to manage every item and eliminate some of the steps usually involved in fulfillment processes. Since it became part of the operations managers’ toolkit, several organizations have had success with cross-docking in recent years.
Companies that have realized new efficiencies using cross-docking include:
- Körber – Using autonomous mobile robots (AMRs) and a new case picking workflow allows Körber to maximize efficiencies and reduce injuries.
- Kroger – As part of their drive for higher efficiency and delivery, Kroger recently opened two new cross-docking centers to act as transfer points for an automated customer fulfillment network.
- Wal-Mart – Sometimes called the king of cross-docking, Wal-Mart delivers about 85% of its merchandise with suppliers and fulfillment departments, all integrated into a single, efficient solution.

To maximize the benefits available from cross-docking, you need to note that implementing it correctly requires meticulous planning and responsive coordination at all points in your supply chain. The companies who’ve made a success of their cross-docking initiatives depend on new technologies and warehouse automation systems integrated into every element of the logistics process.
When is Cross-Docking Used?
While cross-docking works for any kind of logistics and supply scenario, deciding to use this approach depends on the company’s daily operations. When speed and efficiency are key, cross-docking allows distributors who work with perishable goods to reduce waste by ensuring timely delivery.
Other organizations like TJ Maxx can use cross-docking because ensuring that specific inventory reaches every store isn’t a core element of the business. The decision of when and how to use cross-docking depends on your company’s operational model, current business strategy, and technology adoption required in the organization.
What are the Benefits Available from Cross-Docking?
Cross-docking helps companies to streamline supply chains and shorten the time to fulfillment. The entire process depends on efficiently handling the handshake between inbound supplies and outgoing shipments. Similar to how goods pass through major terminals or airports, cross-docking shortens the time that any product sits on the warehouse floor (costing money and taking up space).
Some of the key benefits available from cross-docking are:
- Streamlines the supply chain to reduce inventory handling and storage
- Reduces labor and warehousing costs associated with inventory management
- Allows for faster, more accurate fulfillment when implemented successfully
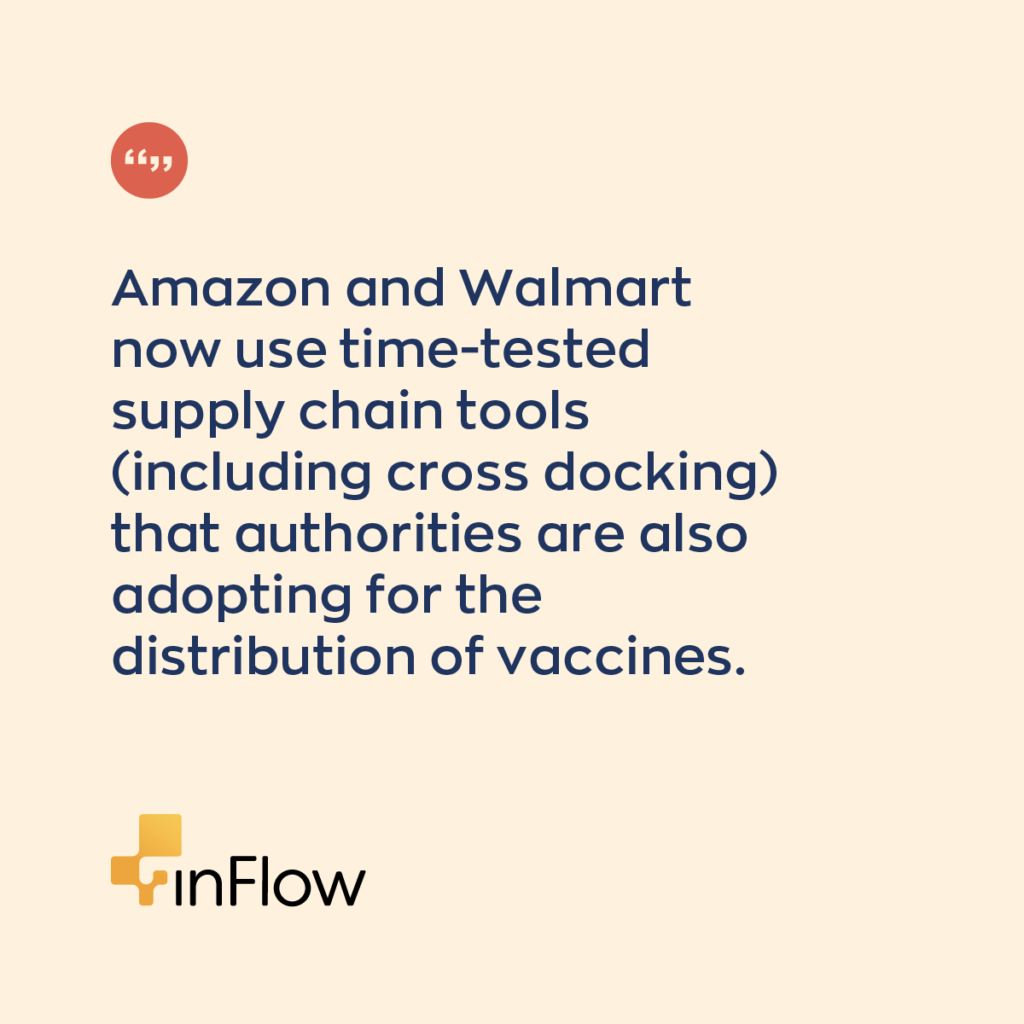
What Are the Main Cross-Docking Types and Techniques Available?
As cross-docking is a management technique for supply chain management and logistics, there are different approaches available. The process gets its name from the idea that companies are moving items from the inbound docks, across the warehouse floor, to the outbound trucks in the shortest time possible.
While this sounds simple, there are different approaches that companies can use today which may be specific to the region, supplier, or goods involved. Here are the three main cross-docking types to consider.
1. Continuous Cross-Docking
The simplest form of cross-docking is when you move goods at a central site immediately from the receiving bay to your fulfillment trucks. Terminals using this method can optimize every portion of the operation to quickly offload and load vehicles, with minimal disruptions or obstructions.
When there’s a slip in schedule, operations managers need to establish rules that guide workers and systems on how to proceed. An example would be that if a scheduled truck doesn’t arrive on time, supervisors shouldn’t promote another truck to the head of the queue, as it may disrupt the preplanned process and cause a bigger delay.
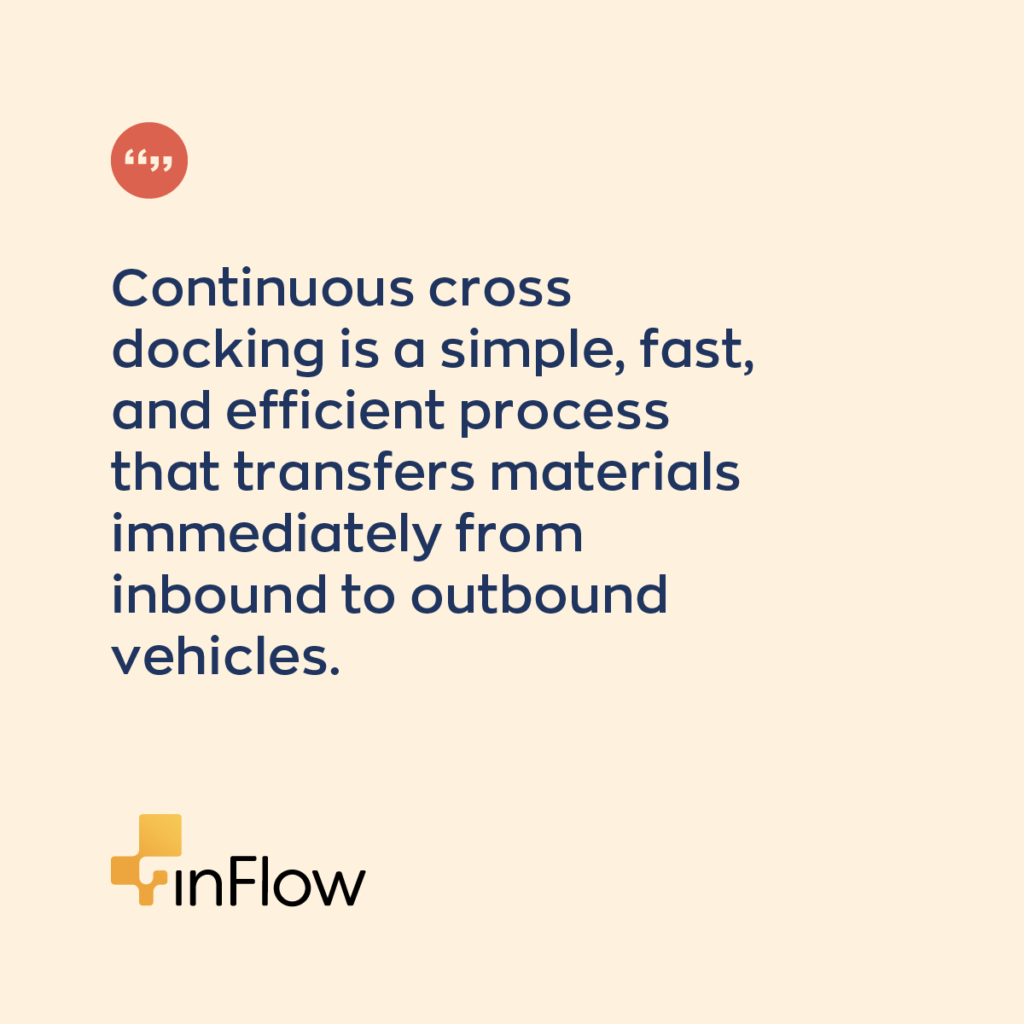
2. Consolidation Cross-Docking
Some situations call for a process where different goods arriving on different vehicles require picking before loading onto outbound vehicles. Consolidation cross-docking allows organizations to make fewer supply trips to different locations by first consolidating inbound items before loading the fulfillment vehicle.
Operators will merge multiple different loads and ensure that all items required for an outbound vehicle are available before releasing the shipment. These types of cross-docking terminals require more storage space than continuous cross-docking facilities. In this way, consolidation resembles a traditional warehousing process but will still be quicker and have dedicated space available to consolidate merchandise for quicker outbound loading.
3. Deconsolidation Cross-Docking
As opposed to consolidation cross-docking, deconsolidation cross-docking is when there are specific products on an inbound vehicle bound for different locations. Instead of waiting for outbound vehicles to have a host of goods, orders specific to a destination receive precedence – and operators separate loads to keep the fulfillment process going. Deconsolidation cross-docking still speeds up the process and usually works in situations where you are dealing with smaller, customer-specific orders.
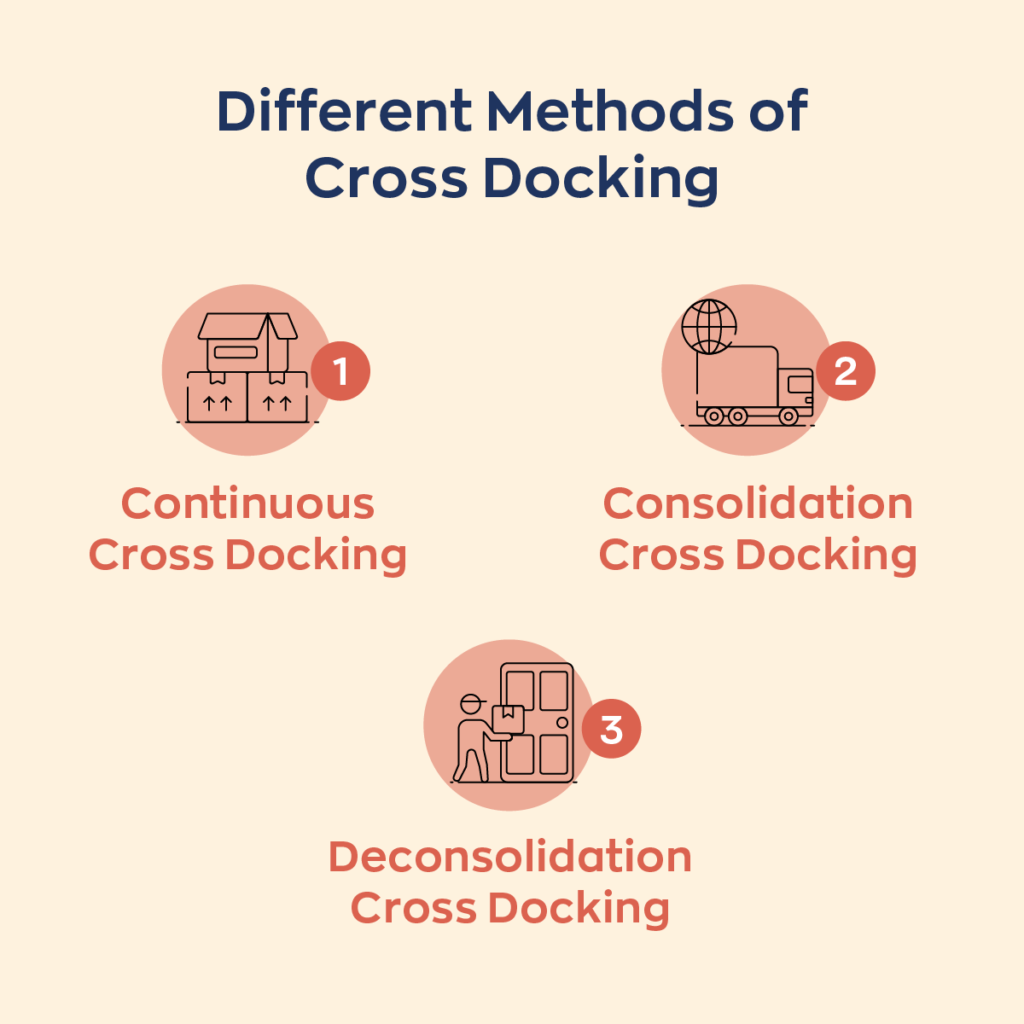
Establishing an Efficient Supply Chain with Cross-Docking and inFlow
Cross-docking is an agile approach to inventory management but depends on your company’s digital transformation capabilities. With greater pressure on global supply chains, the use of technology is a key enabler for suppliers, warehouses, and fulfillment centers.
inFlow provides an integrated platform to manage all your supply chain logistics and inventory processes from a single, connected system. With inFlow, you can access your information on different mobile devices to find real-time insights, and use advanced integration to connect your entire facility to a single platform.
If you’re looking to establish a successful cross-docking process at your facilities, you’ll need to start with smart, effective, and efficient warehouse management tools. inFlow helps you to organize products, identify inventory, manage pricing or sales, and maintain oversight over all your processes.
0 Comments