Inventory issues can strike almost any warehousing operation. These are often most prevalent during busy periods, particularly when you have a small operation. Juggling the challenges can result in adopting “duct tape” solutions. This refers to tactics that are intended to be a temporary fix to an issue.
Problems arise when warehouses perpetuate these duct tape solutions in the long term. This is common for new businesses opening their first warehouse without solid operational protocols. It can also be the result of unexpected growth, when the need to transfer stock between warehouses while coping with sudden order influx can be overwhelming.
It’s important to prioritize the appropriate solutions for your warehouse’s circumstances. Rather than using stop-gaps, you must consider upgrading to inventory systems that meet the needs of your stakeholders. Let’s take a look at some of the common duct tape solutions and how to update them.
Using paper or low-tech systems
Inventory tracking is an essential part of any warehouse operation. With new businesses or those that have become disorganized over time, there is a tendency to go low-tech.
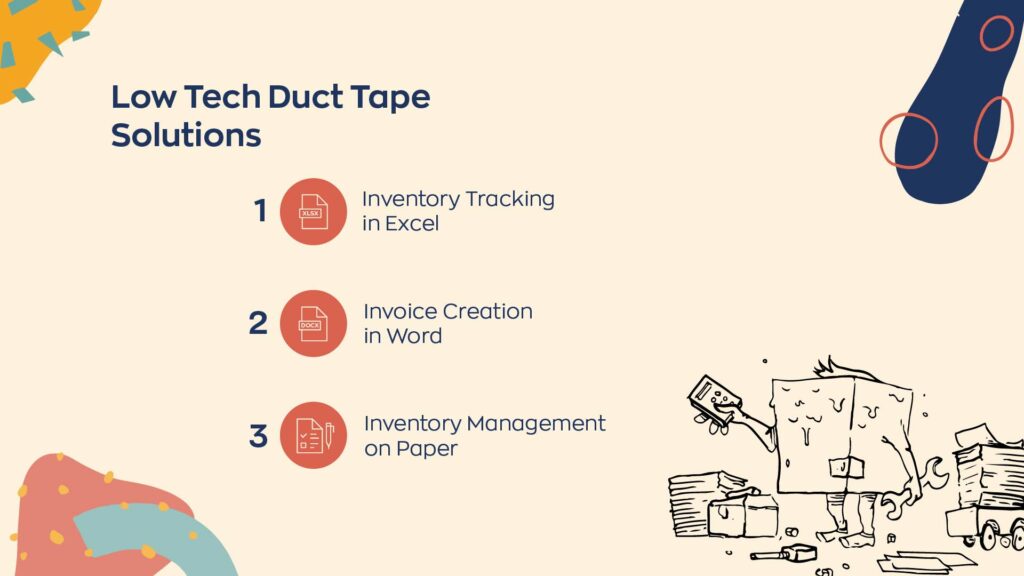
The duct tape methods here tend to include:
- Inventory tracking in Excel: It’s easy to see why some businesses utilize this approach. It’s an accessible and familiar platform to most entrepreneurs. Nevertheless, Microsoft Excel is not suitable for long-term inventory management. It’s more labor-intensive to maintain than most specialist platforms. Not to mention there’s no integration with other areas of your operation.
- Invoice creation in Word: Again, familiarity and accessibility are incentives for relying on this method. Nevertheless, invoicing in Microsoft Word is less efficient than using proper inventory software. There’s no way to track the payment of Word invoices and you can’t link these automatically to report generation platforms.
- Inventory management on paper: Small warehouses may be able to cope with paper inventory management initially. However, this is rife with the potential for human error. Not to mention that as the business grows, the method becomes more unwieldy and disorganized.
As an alternative to this approach, warehouse management software solutions have become quite user-friendly. They’re designed to be more intuitive, and even small businesses can interact with the system via a smartphone. You could even use your phone to scan barcodes if you’ve set them up in the software.This can help eliminate the problems of unfamiliar inventory platforms that require extensive training.
In addition, wholesale distribution software can help managers of growing warehouses track, price, and manage inventory. This solution allows for bulk changes, visibility over the progress of all orders, and direct interaction with consumers.
Neglecting to use advanced inventory management techniques
There are various inventory management techniques, and it can be challenging to establish which is right for your warehouse. The Just-In-Time method of only buying the stock you need when it’s ordered is really only suitable for small retailers. An ABC analysis approach can help growing warehouses identify and prioritize inventory items that make the most money. You could also consider using reorder points for your products to ensure you’re only ordering items when you need them.
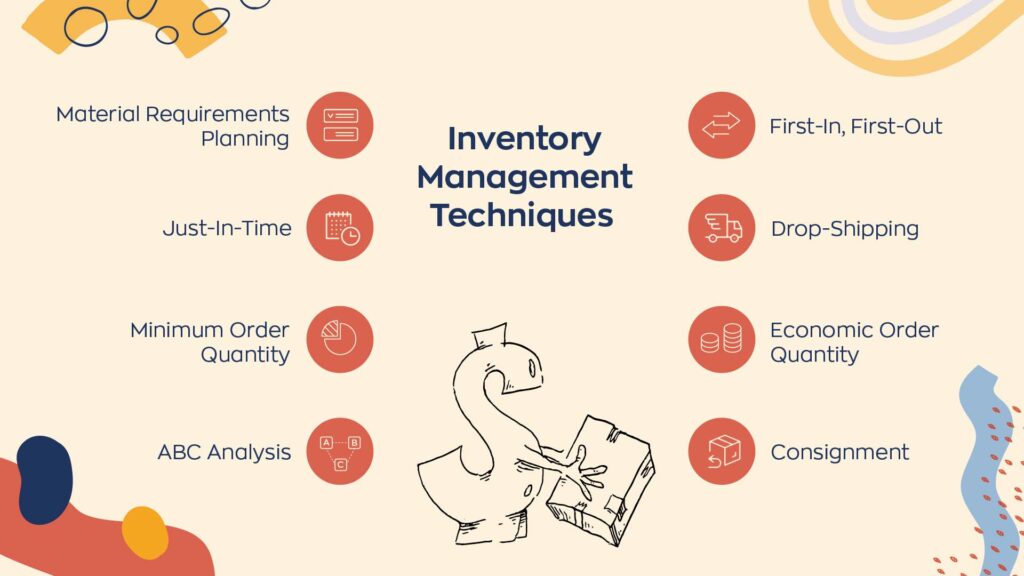
Part of the key here is taking the time to assess where the methods and the equipment involved mesh with your current operations. For instance, many new warehouses track inventory manually using a combination of stock-keeping units (SKUs) and spreadsheets. A barcode system can increase the accuracy of inventory tracking without negatively disrupting current operations. This process also integrates well with more advanced warehouse management software that can support your business’s continued growth.
As with any scaling, you don’t need to implement new practices all at once. However, committing to making gradual upgrades gives you and your staff the methods to innovate and succeed.
Piling up excess stock
One of the common duct tape practices new or less-organized warehouses can fall into is excess stock accumulation. This isn’t a particularly efficient approach to inventory management. Indeed, piling up too much safety stock tends to be environmentally unsustainable as it uses unnecessary resources and can contribute to waste. Warehouses are already among the primary contributors to greenhouse emissions. It’s important to behave responsibly.
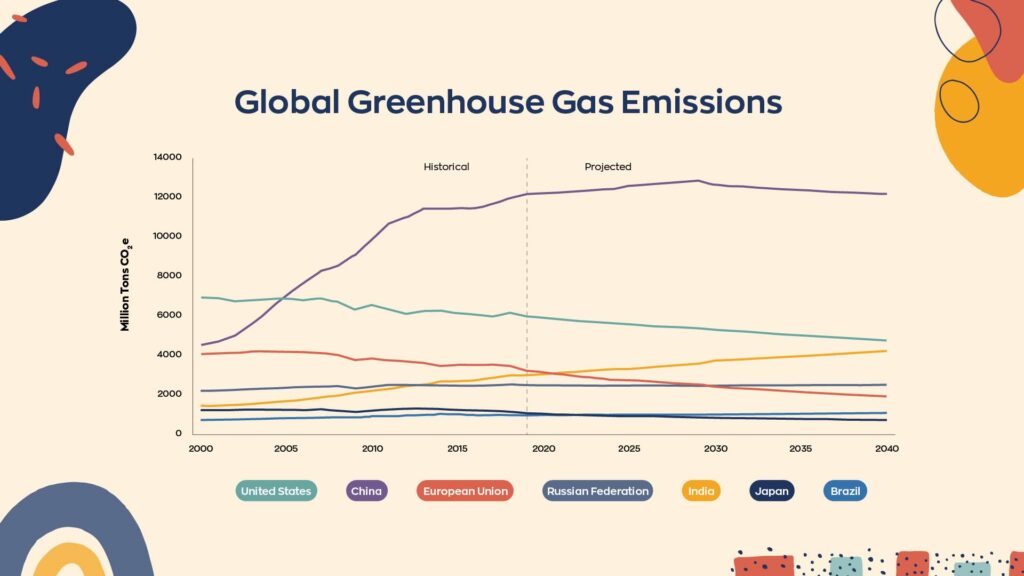
This isn’t to say you shouldn’t have some additional stock in place — after all, safety stock reduces the risk of running out of inventory at peak demand times — but you need to utilize effective management protocols. Firstly, make sure your stock numbers are based on solid and continual market research to assess demand. Importantly, use inventory management software that tracks your average order and lead time data to predict sensible safety stock numbers.
You should also adopt green methods for handling your safety stock. Keep track of the age of the items in the warehouse. Create protocols to recycle and reuse goods that have become obsolete or past their prime. This could include working with manufacturing partners to sell back items with reusable components. It may be donating stock to charities. This is not only environmentally sound, you can also use these donations to benefit from tax deductions.
Not optimizing warehouse space
The property you choose for your warehouse is a vital component of your business. Many new companies are in such a hurry to get started that they take the duct tape approach of improvising their use of the space. Indeed, during unexpected growth periods, there can be a panic to just squeeze shelving or equipment wherever you can fit them. However, this doesn’t make the most of one of your business’s most valuable assets.
Space efficiency in warehouse management isn’t just about maximizing places to store inventory. You also need to consider how the space is used and how things flow between spaces. Remember that optimizing your warehouse isn’t a one-and-done activity. Your operations will develop over time. As such, it’s important to perform a space efficiency assessment at least once a year. Being methodical and analytical in your approach can support the long-term efficacy of your warehouse.
Keeping employees siloed
When discussing warehouse management practices, there is a tendency to focus on the processes and tools. However, employees are often treated without sufficient consideration as a warehouse grows. The duct tape approach, particularly with new businesses, is to silo staff. This is where employees are hired in a reactionary way as the need arises. The result being there aren’t tools in place to help staff be a more connected, collaborative, and effective team.
When you make consistent efforts to bring your team closer together, everyone benefits. Some approaches you can consider here include:
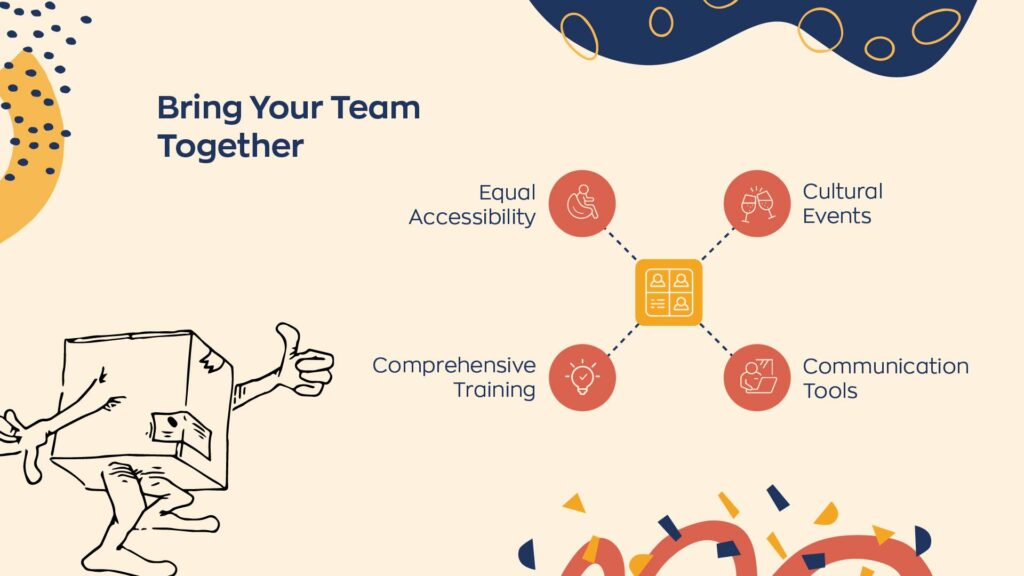
- Communication Tools: Even with a smaller warehouse, your staff may be working in different areas. Providing walkie-talkies empowers them to collaborate more efficiently. If your company is large enough to have more than one warehouse, utilize software that incorporates multiple users across your network.
- Cultural Events: Your staff are human beings as well as talented professionals. Holding regular company-wide fun cultural events can be an important way to boost morale. Most importantly, it helps your employees to get to know one another and develop stronger bonds. This can result in better worker retention and more productive teams.
- Equal Accessibility: One of the best ways to make sure staff are connected is to make your workplace accessible for all of them. This way, staff with differing needs and personal challenges don’t feel excluded. This can include using clear images as well as words on warehouse signage. It should also involve performing regular accessibility assessments across your physical space and your digital tools.
- Comprehensive Training: Good training practices create standardization within your company. This ensures that everyone on the team is on the same page when it comes to business processes.
Wrapping up
Duct tape solutions are usually a response to unexpected and challenging situations. Unfortunately, relying on them for too long is inefficient and may hamper your warehouse’s development. The key to growing without becoming overwhelmed is taking a step back to assess and plan. Take regular and honest assessments of what your upcoming needs are. Think logically about what software and methods best address them not just now but in the long term. Keeping a level head and making well-considered decisions is always a more impactful approach.
0 Comments