A cycle count is one of many methods for counting your inventory. During this process, a business breaks its inventory into different categories, then regularly counts the amount of available product in each category. For example, the organization might count the number of TVs in their warehouse followed by the number of phones.
These counts could be done monthly, weekly, or even daily, and over time they account for the whole warehouse. Along with inventory recording, this helps to get a full, and more detailed picture of a warehouse’s inventory.
How is inventory cycle counting different from inventory recording?
Cycle counting relies on small-scale, repetitive counts in order to provide an accurate snapshot of inventory levels. This takes place at set intervals over time. By focusing on smaller groups individually, cycle counting provides a more granular look at the overall inventory, allowing a business to identify errors or discrepancies as soon as possible.
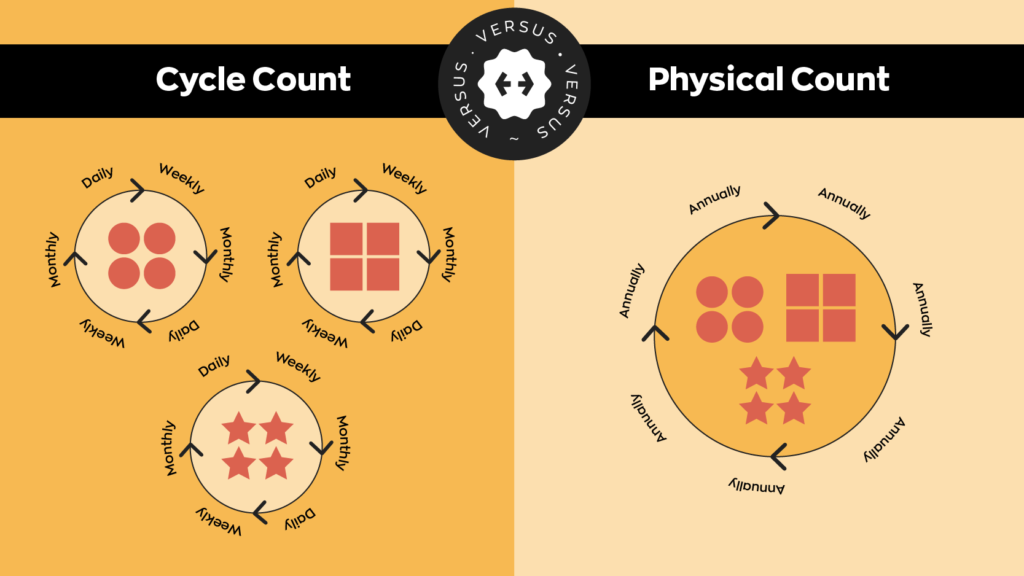
Inventory recording, on the other hand, keeps track of every movement of every item within the warehouse, which helps to keep a running, accurate inventory count. The ongoing nature of inventory recording means that it requires detailed documentation to be most effective. As a result, it’s useful to employ multiple counting methods to reduce potential miscounts or other inaccuracies.
What are the benefits of cycle counting?
The cycle count process has a number of benefits over physical counting. Here are the big ones:
- Less disruptive: Cycle counts are smaller and require less manpower to perform than full physical counts, which means that businesses can operate normally during cycle counts, reducing facility downtime.
- Higher accuracy: Counting a smaller amount of inventory each time, with more individual counts, helps to ensure the accuracy of inventory counting. A shorter period between taking inventory can also help to provide more current information that can inform other important decisions.
- More informed purchasing decisions: Having more detailed and accurate records means that you’re much less likely to purchase inventory that you don’t need. This can free up capital in the short term and prevent waste in the long term.
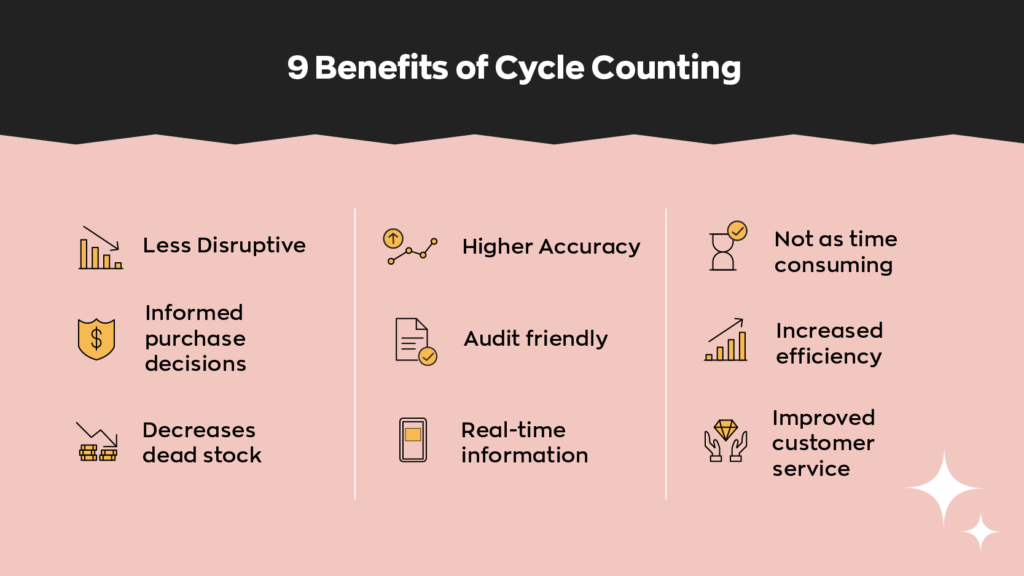
With all this in mind, however, it’s important to note that cycle counting is not a replacement for physical counts. Cycle counting can serve as a helpful companion that works together with these counts to provide more accurate overall information.
Are there different cycle count methods?
There are a number of different cycle count methods, which can be broken down into different categories:
- ABC counting: In this common form of cycle counting, products are labeled A, B, or C depending on their level of importance. For example, products labeled “A” may be of high importance, and as a result, are monitored more frequently than B or C products.
- Random sampling: Instead of operating based on a system, products are counted at random until the cycle is complete.
- Opportunity-based counting: In this method, businesses perform counts at “important times,” such as reorder periods.
Because of the diverse needs of different businesses, there is no one method that works best in every instance. A business may also decide to employ different types of counting for different needs, such as changing methods during busy periods, or in order to adapt to inventory growth.
Cycle count inventory implementation and best practices
An inventory cycle count may be more efficient than a physical count, but shouldn’t fully replace them. When implementing cycle counts into your workflow, it’s best to perform a physical count beforehand. This way, you know that you’re starting off with an accurate count.
Best practices tend to differ from industry to industry, but there are some that should be useful for most businesses to follow.
- Stop inventory movement: Processing orders during the process can lead to inaccuracies. This can cause a ripple effect with further issues later on, and more work down the line.
- Keep information up to date: Whenever you receive new inventory, make sure to register it in your inventory management system. Otherwise, you’ll end up with greater discrepancies.
- Perform annual physical counts: It’s still best to perform annual physical counts to create an accurate starting point for the year.
- Set a schedule and stick to it: Repetition is key. This process should be performed quarterly at a bare minimum.
- Don’t give up: Even if you end up lacking the resources to perform regular counts, don’t stop doing cycle counts altogether. Instead, learn to prioritize and track higher-value inventory.
- Alternate staff: The cycle count process can be tedious. Alternating between teams keeps people from burning out, and could stifle any potential thievery.
The important thing is to find what works for you. Different businesses need different things. Find your flow and stick to it. A system that works for one business might not work for yours, and vice versa.
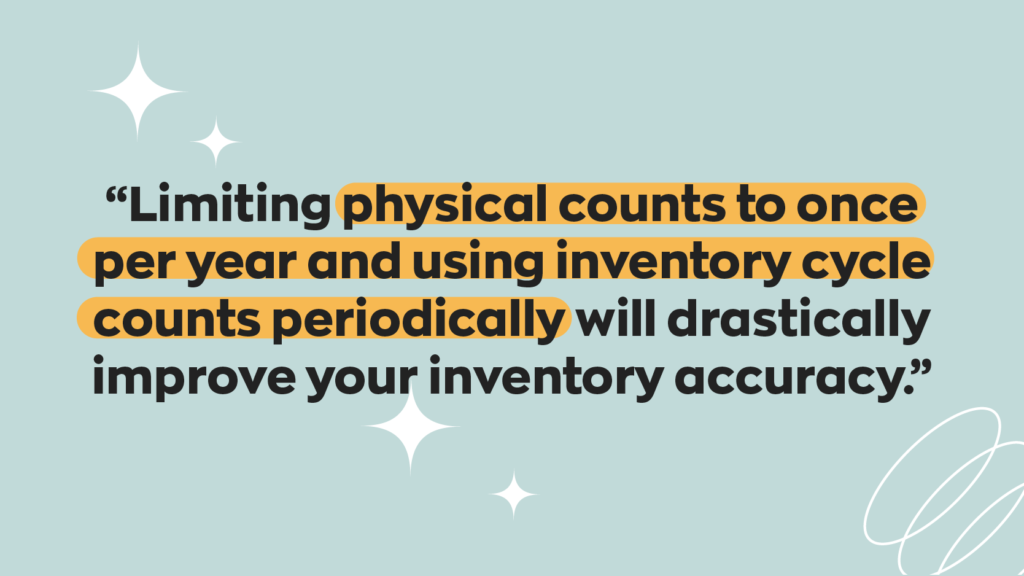
Using software to help with cycle counting
Counting inventory is an important part of warehouse management, but it can be time-consuming and labor-intensive. At the same time, that doesn’t mean there’s no way to make it easier. According to a report from the Business Continuity Institute, more than 57% of businesses currently make no use of technology for supply chain management.
Software like inFlow for inventory management can help make things easier by giving you a starting point. Instead of gathering a list of products and creating your own sheet, inventory management software can do it for you.
Inventory management software can help to automate some aspects of the process, such as updating multiple sheets. Software like inFlow streamlines the process, but it’s important to note that the inventory cycle count process still relies on manual labor.
0 Comments