We’ve talked before about the importance of material requirements planning (MRP) and how it saves manufacturers time and money. A master production schedule (MPS) serves a similar purpose, but there are some important distinctions between the two. Today we’ll be explaining that difference and answering some other questions along the way.
What is an MPS and how is it different from production scheduling?
A master production schedule is exactly what it sounds like; a schedule that lays out what numbers your production line should be hitting and when. At first glance, these two processes might seem identical, but there’s a key difference. Production scheduling answers the what, while a master production schedule answers the what, when and how much.
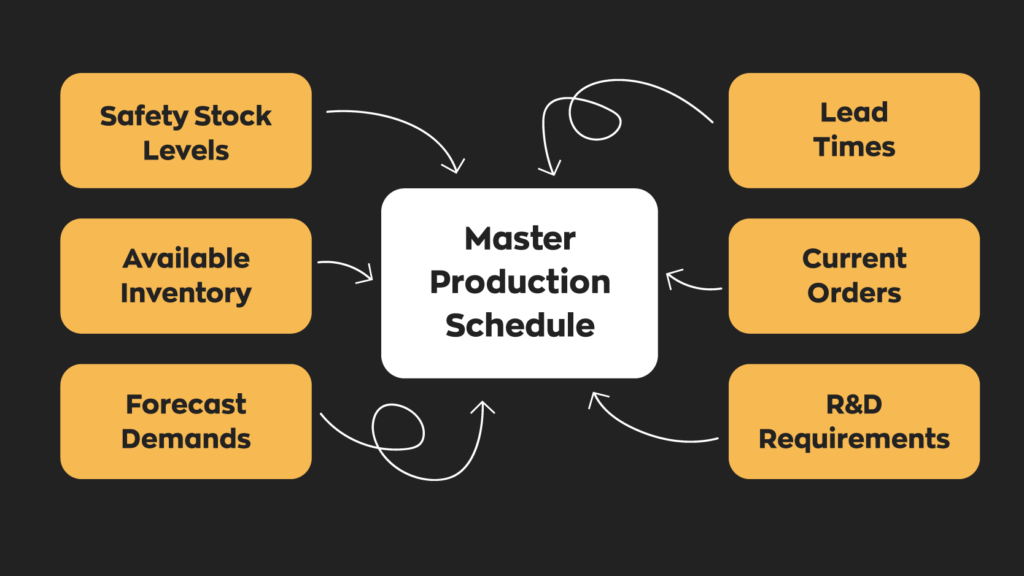
A big part of production scheduling is figuring out the number of materials you’ll need to complete a production cycle. On the other hand, a master production schedule tells you what materials you should be using and when. It’s really exactly what it sounds like: a schedule. It tells businesses what they should manufacture, when, and how much to manufacture.
Why is a master production schedule important?
There’s a lot of reasons why an MPS is important for businesses. There’s a handful of factors at play, but many of these reasons stem from one factor. The manufacturing process adds a lot of moving parts to a business.
Businesses that buy and resell products really only need to keep track of a few things. Inventory levels, as well as what goes in and out of the warehouse. This is an oversimplification, but it helps put things in perspective.
Businesses that manufacture their own product have to track all of this on top of the manufacturing side of the business. This includes things like input and output, cost, production time, production costs, and so on.
A master production schedule doesn’t outright solve issues that pop up, but it goes a long way in alleviating them. It serves as a reference point, telling businesses where they should be in the production cycle and when.
What are the benefits of a master production schedule?
A properly calculated and implemented master schedule is one of the most useful tools a business has at its disposal. It offers a plethora of benefits both big and small. We could sit here all day listing them (seriously, we could!) but at the end of the day, the fact of the matter is that planning ahead is just good practice. Without the foresight to plan ahead, businesses would fall apart.
For manufacturing companies, a master schedule serves as both a reference point and a communication tool. Making sure manufacturers have a schedule ahead of time helps minimize back-and-forth while ensuring that production is on track.
Planning ahead also allows manufacturers to stock up on components early. This can help save on money in the long run, as the price of materials tends to fluctuate regularly. This makes in-the-moment orders more feasible, allowing businesses to take advantage of a sudden spike in demand.
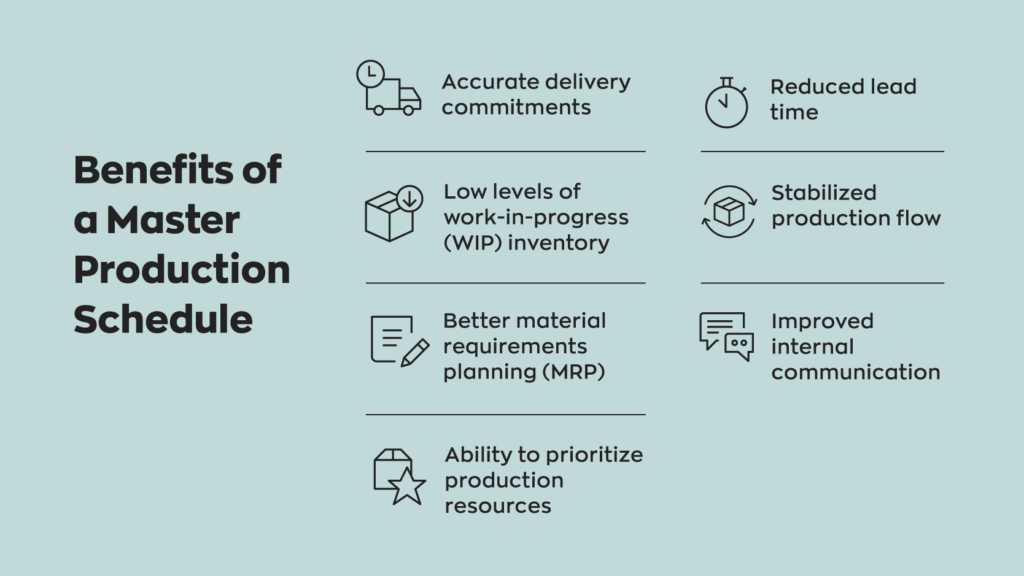
There are also some benefits on the human side of things as well. Coming to a long-term agreement helps keep manufacturers in business, which may make them more willing to help out if you find yourself in a bind.
How do you create an MPS?
If you’re looking to create your own master schedule, here are some basic steps to follow. Keep in mind that different businesses have different needs– what works for other businesses might not work for you.
Calculate expected demand. Figuring out demand is more important for manufacturers than sellers, due to the additional costs of the manufacturing process.
Figure out the raw materials needed. Also known as a bill of materials (BOM), this is an important part of the process. It’s also a good idea to calculate the long-term costs in order to take advantage of any market shifts. This can also help plan for anything unexpected.
Develop a master plan. Before developing a plan, make sure you have all the information you need. Rushing into production opens the door to a wide variety of issues, both long and short-term.
Maintain it. For the most part, a master production schedule isn’t something that you can set and forget. It requires careful monitoring in order to ensure that the demand forecast is being met.
How do master production schedules fit into the bigger picture?
Considering all the other business systems out there, you might be asking: where does this fit in? We briefly touched on it earlier, but a business is composed of many moving parts. Managing these moving parts is the key to operating a successful business.
In the modern day, while there are more moving parts than ever, there’s also many more ways to manage them. In that sense, an MPS is like inventory management software: a tool that businesses use to keep track of things.
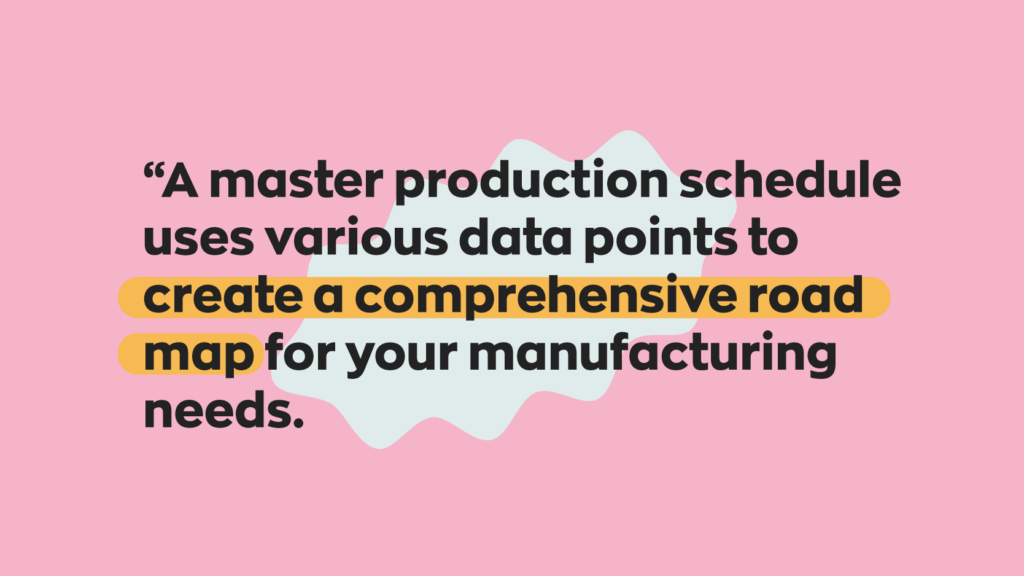
Keep in mind, though, that the nature of master production schedules means that not every business needs one. If your business doesn’t deal with the manufacturing side of things, there’s simply no need for a production schedule. It’s something of a specialized tool; not every business needs it, but the businesses that do need it really need it.
What tools can help with a master production schedule?
While there is software to handle the manufacturing side of things, it’s perfectly possible to make do without. There’s a couple of reasons for this.
First, while creating a master production schedule seems challenging, it has more to do with using information that already exists. There’s nothing wrong with using software to analyze trends, but its necessity is a bit of a toss-up.
Second, much of today’s available inventory management software already offers manufacturing features. It might not create an entire schedule on its own, but it’s simple to figure out what works going forward. Because of this, if you’re already using inventory management software, there’s not much point in paying more for MPS software.
For example, inFlow offers a suite of manufacturing features. For bill of materials (BOM) assemblies, users can create work orders from invoices, while our perpetual management system updates things in real time. One look tells you the cost of manufacturing, as well as how many units you can make.
0 Comments