We’ve previously talked about what an enterprise resource planning (ERP) system is, and how they relate to inventory management systems. Without going into too much detail, an inventory management system is a small (but important!) part of ERP systems. In this sense, material requirements planning, MRP software, is similar to an inventory management system. They’re both part of ERP systems, and both serve a similar purpose.
If you’re one of those people who would rather watch and listen than read, then check out this short clip from our podcast for a brief overview of material requirements planning (MRP).
Read on for a more in-depth look at what an MRP system is, who uses them, and why they’re so important.
Who uses material requirements planning (MRP)?
This might seem a bit out of order, but it’s easier to explain the who before the what. It’s also important to keep in mind that not every business that needs an inventory management system needs MRP.
Broadly speaking, every business that sells products fall into one of two categories. They either purchase and resell products, or they are one of the growing manufacturers that produce their own. Businesses that manufacture their own products face their own unique issues– which is why they use an MRP system.
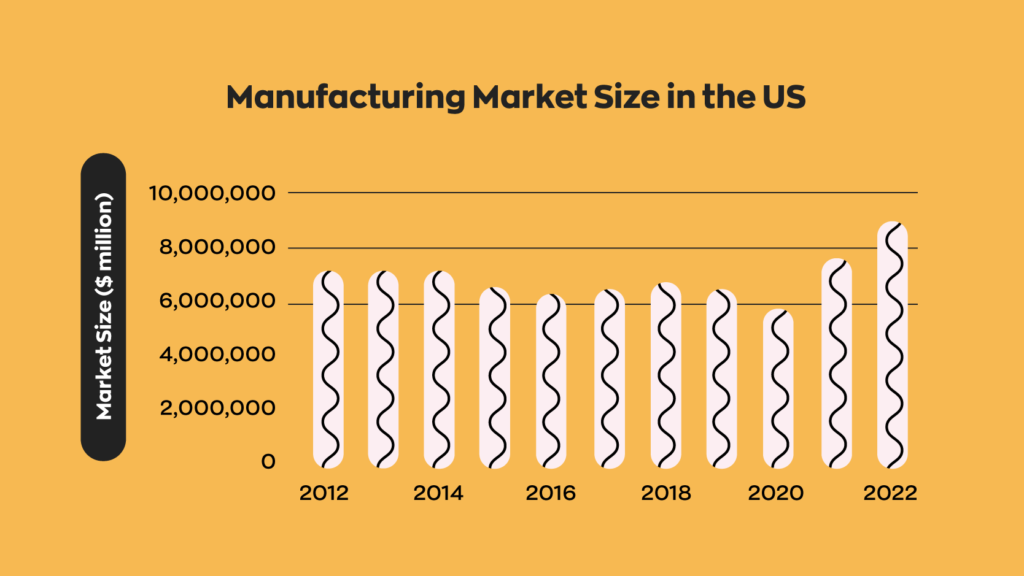
What is MRP?
As the name suggests, MRP is the process that businesses use to keep track of manufacturing materials that they have on hand. This is usually some sort of MRP software, but some businesses do things the old-fashioned way. Businesses use this information to plan out their manufacturing process. The objectives of MRP systems vary from business to business, but they generally fit into a few categories.
What can MRP software do?
Track input and output- the law of manufacturing is simple. Put something in, get something out. That might be an oversimplification, but there’s some truth to it. If the input and output aren’t monitored, something could fall through the cracks, leading to a net loss.
Track material supplies- most products are made of more than one component. If you’re not careful, you may find yourself in a position where you might have one part but not another, forcing you to halt production. Keeping track of supplies ensures that you won’t run into this problem.
Calculate potential output- because most products are made out of more than one component, there are more variables to consider. This makes it difficult to figure out how much of a product you can produce at any given time. For a human, at least. MRP software can calculate whether or not you have the required components on hand to fulfill a bill of materials (more on BOMs later).
Consolidate information- a recurring theme within the business industry. Remaining informed is an important part of running a business. If you scatter information across many different places, it’s difficult to get a clear picture of what’s going on at any given time. MRP software keeps things organized, offering a clear report at a moment’s notice.
Bill of materials (BOM)- rather than a task, this is a product of MRP. A bill of materials is really just a fancy name for “ingredient list.” A BOM lists the required materials and calculates the cost of those materials to reach a certain output.
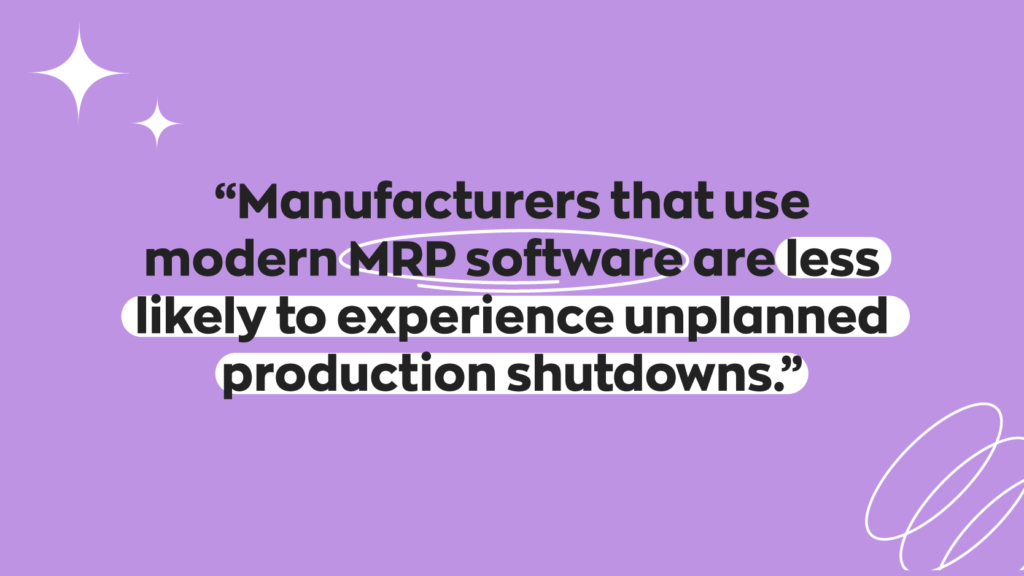
Why is MRP software so important?
MRP software and inventory management software might be similar to each other, but they have different use cases– and rarely would one replace the other.
The purpose of MRP is similar to an ERP system: optimize business operations. That’s a broad statement, though, and it’s important to note that MRP systems operate on a much smaller scale. We said it once before, but it’s worth saying again: businesses that manufacture goods in-house face a variety of challenges.
Even if the manufacturing process is simple, there are a lot of other variables to consider. How long does it take to manufacture one unit? What components does it use? Are some components used up faster than others?
For example, to illustrate our point, let’s say that your company sells toy trucks. To make each truck, you need to piece together the body of the truck along with the wheels. A single truck requires one body and four wheels, so essentially, you’re using up the components at a 1:4 ratio. Not only are you using these parts at different rates, but they also cost different amounts.
For this single example, that’s already three things you have to keep track of. The number of truck bodies and wheels used, the output of both materials, and the two different prices. And this is just for one product– imagine keeping track of 60 products like this.
All of these variables mean that it’s really (really) hard and really time-consuming to figure things out on your own. Even if you’re good at math, chances are MRP software is better.
What are the benefits of (good) MRP software?
As with other systems, it’s important that they’re implemented correctly. This is arguably even more important for MRP because of how many variables it deals with. If something doesn’t work right or breaks somewhere down the line, it can cause long-lasting damage.
With that said, good material requirement planning bring two main benefits:
Production planning- with MRP software, you can spot component bottlenecks before they become an issue. This allows you to create manufacturing plans without worrying about a component shortage.
Resource planning- raw materials are the most important part of the manufacturing process. On top of that, it’s essential to know what equipment is required at what time. This helps businesses optimize their workflow, increasing their overall productivity.
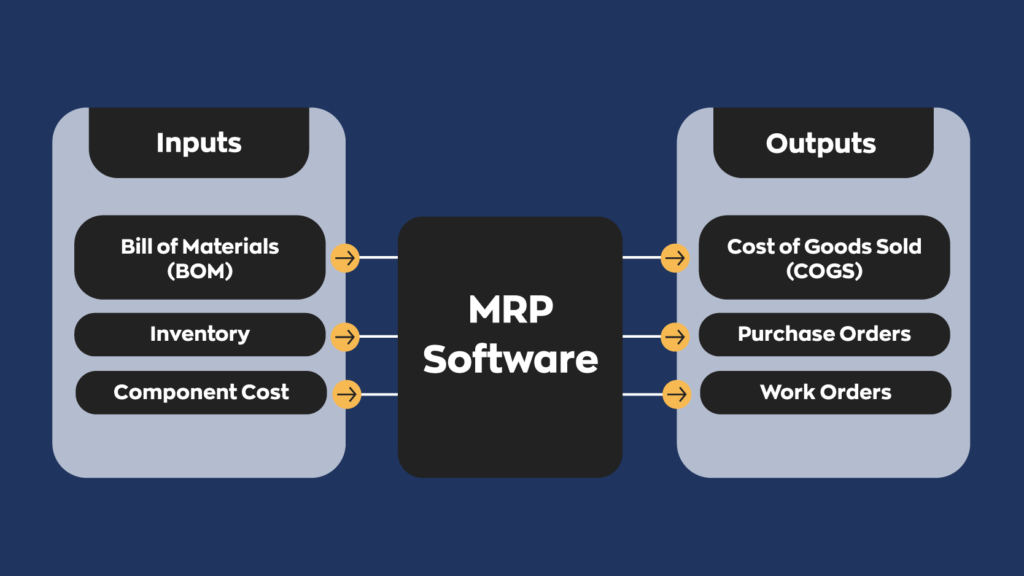
What can you use to improve material requirements planning?
MRP systems can typically be broken into two parts: inventory management and production planning. While these two factors are arguably of equal importance, MRP requires having an accurate inventory count. So make sure you have a good inventory management system!
inFlow is a robust inventory management system that utilizes bill of materials (BOM) with a built-in all-in-one barcoding system. We also have BIG plans to improve our manufacturing features even further in the first quarter of 2023. So be sure to keep an eye out!
0 Comments