Manufacturing is a tricky business, especially when trying to calculate total manufacturing costs. The process itself introduces a myriad of variables, ranging from input and output to direct and indirect costs. As a result, it’s a good idea to know how to use the total manufacturing cost formula.
Today, we’ll be delving into the total manufacturing cost formula and how to use it.
If you like this formula or formulas in general you’re going to love our Inventory Formula Cheat Sheet! We put together 7 of the most commonly used formulas for inventory management in this handy document for anyone to download.
What is the total manufacturing cost formula?
The total manufacturing cost formula itself is pretty simple. It looks like this:
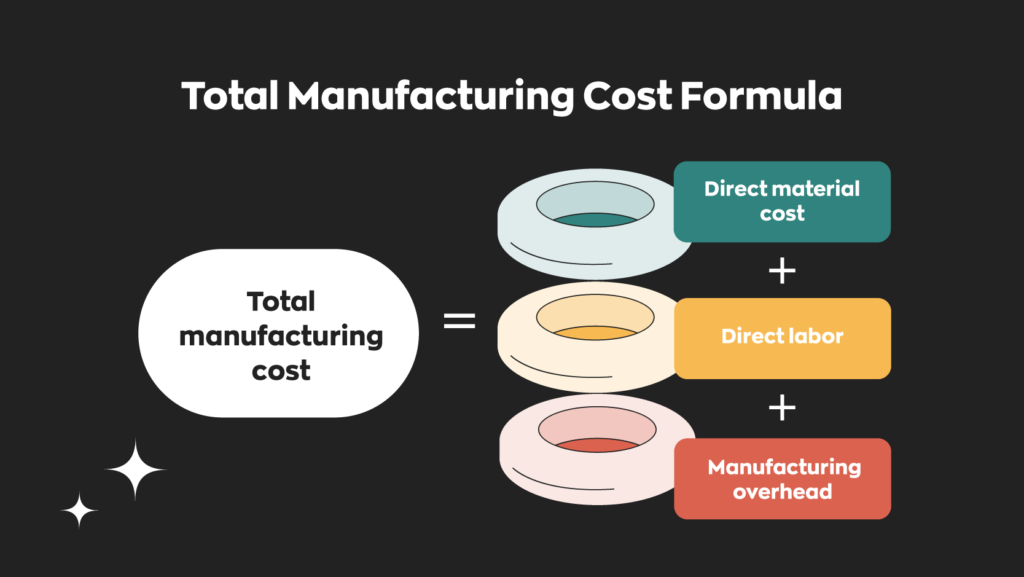
You’re probably wondering what all those terms mean, and we’ll get to that. But before talking about the total manufacturing cost formula, it’s essential to know about direct and indirect costs.
Direct costs refer to any spending directly tied to the manufacturing process. This includes (but is not limited to) labor and material costs.
Indirect costs refer to any necessary spending not directly connected to the manufacturing process. This includes (but is not limited to) the cost of electricity, rent, and so on.
It’s important to factor in both your direct and indirect costs when using the total manufacturing cost formula.
How to calculate direct material cost?
Direct material cost is the first component of the total manufacturing cost formula. Direct material cost refers to the cost of materials used in the manufacturing process. Businesses calculate this by adding the cost of material purchases to the cost of starting inventory and subtracting the cost of ending inventory.
For example, if a company starts with 10 production kits, purchases 20 more, and ends with 5, the direct material cost is the value of 25 production kits. For the sake of this example, let’s pretend that each assembly kit consists of $200 in raw materials. This puts the direct material cost at $5000.
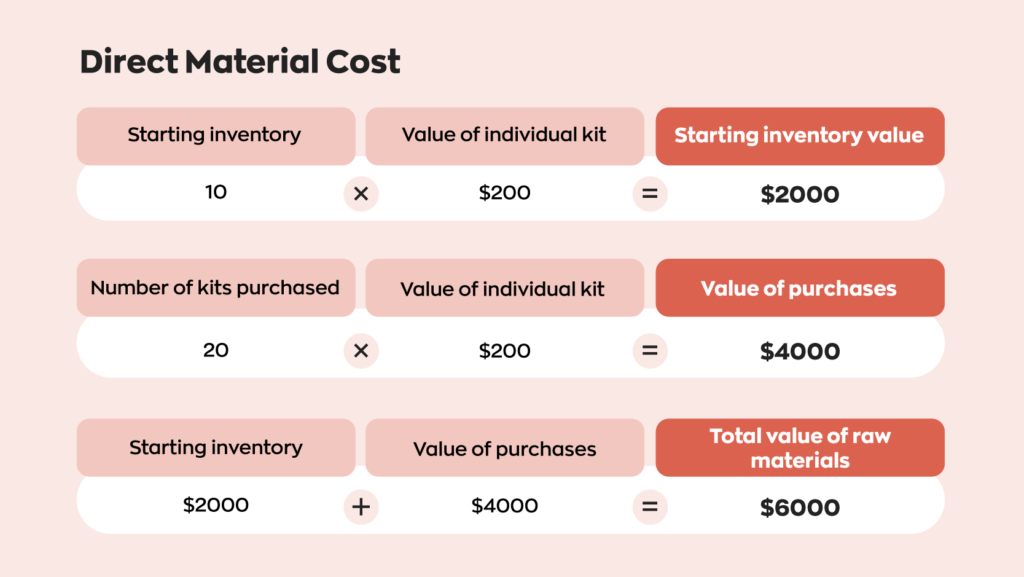
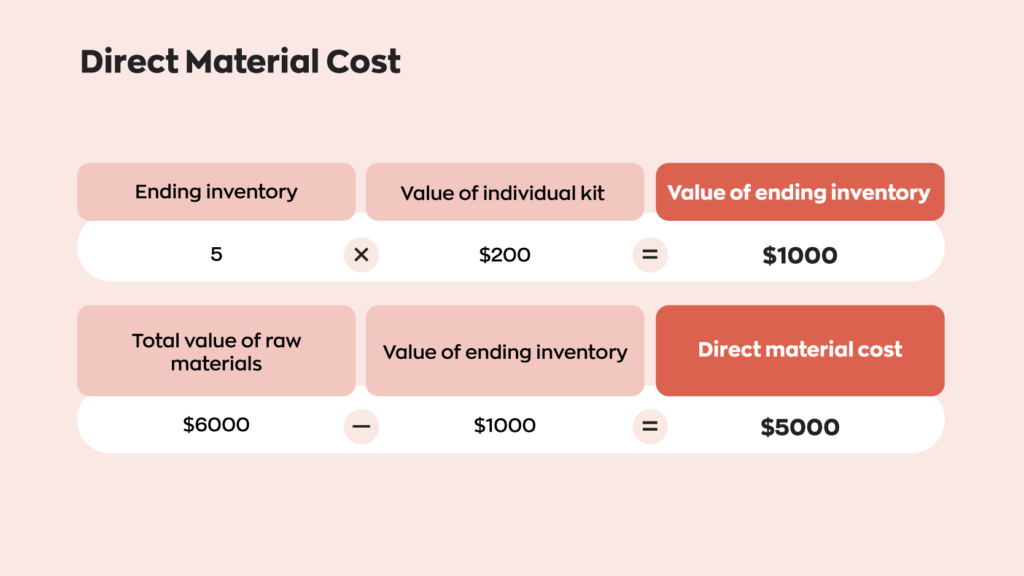
This calculation isn’t necessarily complicated, but there are a lot of variables at play. And this is before even considering that there might be multiple production cycles going on at once.
More cycles mean more variables, which ultimately makes it harder to keep track of things. It’s one of the reasons having a bill of materials system is helpful. It puts all the information in one place and keeps track of everything, so you don’t have to.
How to calculate direct labor cost?
Direct labor costs are the second component of the total manufacturing cost formula. Direct labor cost refers to the salary or wages a business pays its workers during the manufacturing process. Companies calculate this by multiplying the pay rate by project time.
For example, if a manufacturing project requires 40 hours of work/week from a worker paid $25/hour, and the project takes 4 weeks, the direct labor cost is $4000.
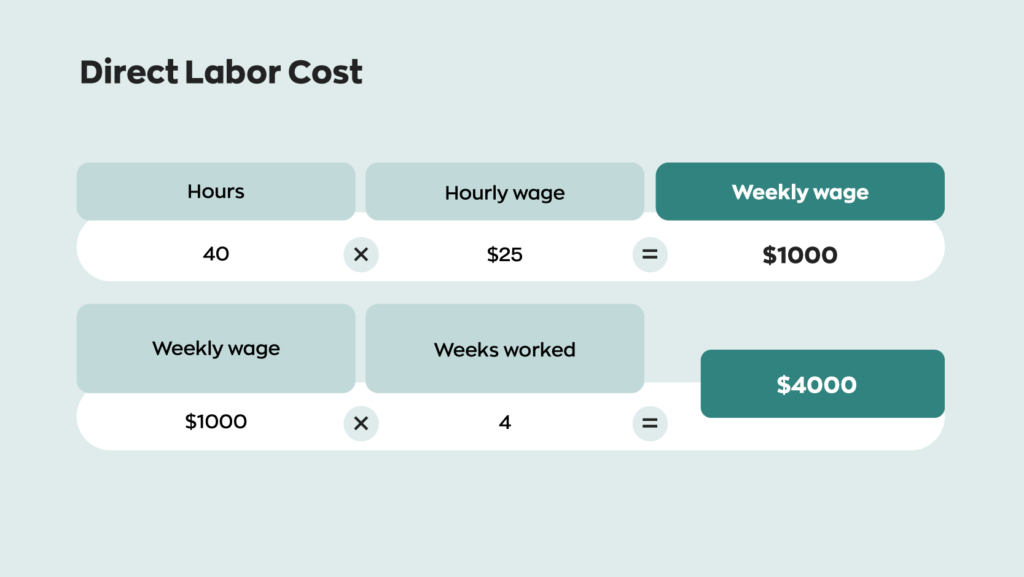
This may seem simpler than calculating material costs, but remember that different employees have different rates. You’ll probably also need more than one employee per project– we just used a one-person example here for simplicity.
How to calculate manufacturing overhead?
Manufacturing overhead is the final component of the total manufacturing cost formula. Manufacturing overhead (MOH) refers to expenses on external costs, like electricity, rent, insurance, maintenance costs, etc.
For example, pretend that a business spends $400/month on rent, $200/month on utilities, and $150/month on maintenance. Their total manufacturing overhead cost is $750/month.
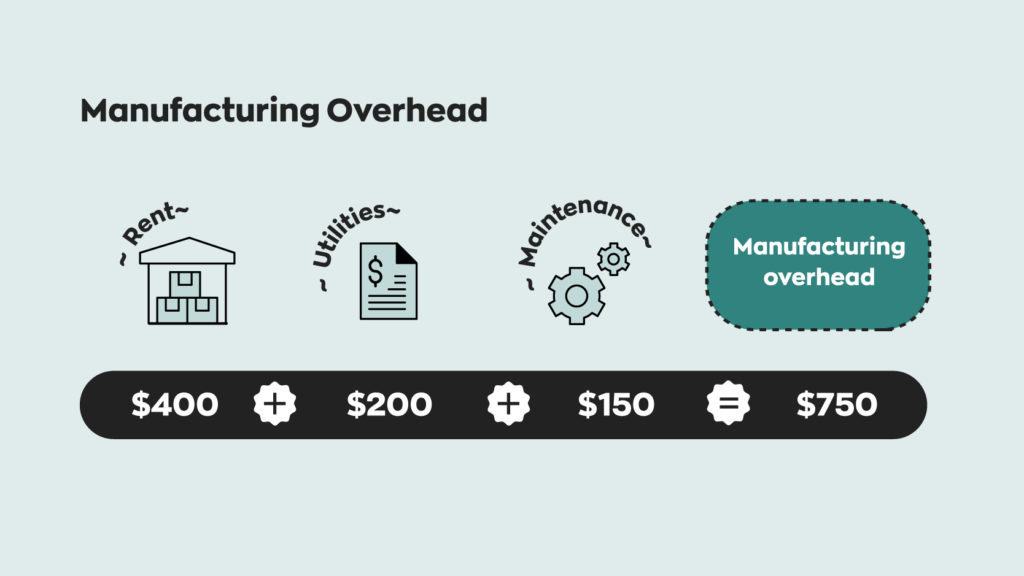
How to calculate total manufacturing cost?
Now that we’ve calculated our direct material cost, direct labor cost, and manufacturing overhead, we’re ready to input these numbers into the total manufacturing cost formula.
$5000 (direct material cost) + $4000 (direct labor cost) + $750 (manufacturing overhead) = $9750.
Keep in mind that these examples (and their respective values) are completely made up. Different businesses have different needs, and as a result, no two businesses will have the exact same manufacturing cost.
There are also other (very important!) parts of these equations to account for. We’ve ignored these indirect costs for the sake of simplicity, but you really shouldn’t. Things like taxes, overtime pay, and so on.
Why is the total manufacturing cost formula useful?
At the end of the day, businesses run on two things: time and money. This remains true whether your business manufactures its own products or not. Keeping an eye on things lets you know if you’re using your allocated funds efficiently. This can pave the way to improvements across the board.
For instance, in the example above, after the production cycle, our imaginary business has 5 assembly kits left over. This isn’t a big deal– they’ll be used in the next production cycle– but until then, you’ll have $1000 worth of inventory just sitting around collecting dust.
If this becomes a recurring (and consistent!) pattern, a business can adjust its order numbers to be more exact. In the long term, this might not make a difference. But short-term, it frees up resources that can be used elsewhere.
Monitoring the total manufacturing costs across different branches can also provide valuable insight. One branch may be overworked, while the other has staff to spare.
How to use the total manufacturing cost formula to decrease costs?
The total manufacturing cost formula will show you where you’re spending the most. Once you have this information, you can focus on bringing down those costs. There are a few ways to decrease total manufacturing costs. You could downsize, work with razor-thin margins, or cut corners in the manufacturing process. However, all of these options have their downsides.
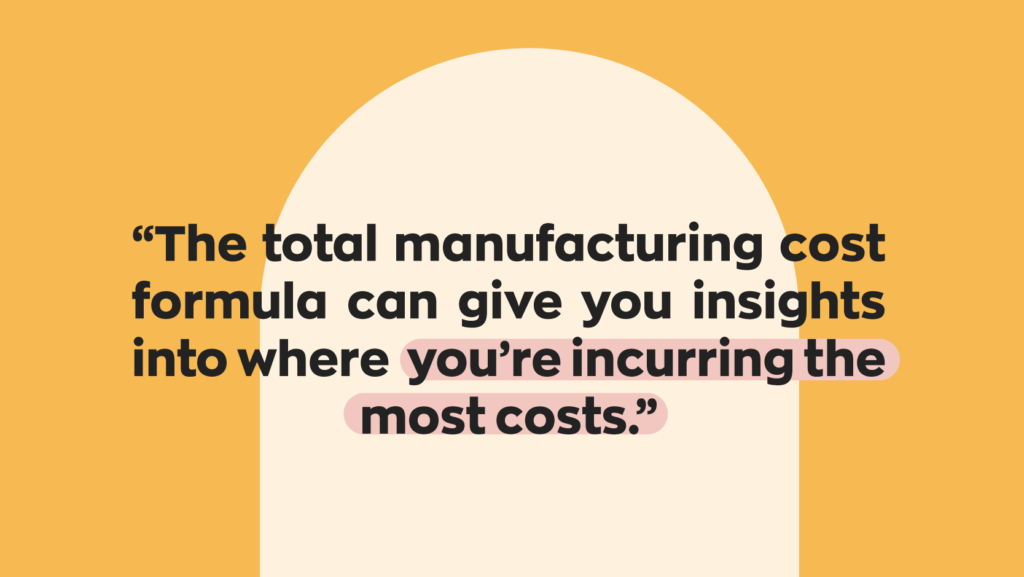
Downsizing increases the risk of running short on manpower. Working with razor-thin margins is a hazard in itself, and cutting corners (more often than not) leads to a noticeable drop in product quality.
As such, the best way to reduce your total manufacturing costs is by increasing the efficiency of the manufacturing process. There’s a lot of ways to do this, but in today’s digital age, that usually means automating.
If you like this formula or formulas in general, you’re going to love our Inventory Formula Cheat Sheet! We put together 7 of the most commonly used formulas for inventory management in this handy document for anyone to download.
Download your inventory cheat sheet now!
Automate- with inFlow!
Something that business owners quickly learn is that businesses run on money. This isn’t hyperbole, either. In one way or another, every part of a business costs money. You need to pay employees, purchase (and maintain) inventory, and so on. If you’re running ad campaigns, even selling your inventory costs money!
Whatever time a business spends on a task has a monetary cost. It might be difficult to calculate– and it might be difficult to see– but it exists. It’s how automation saves businesses money.
Software systems can complete repetitive, menial, and time-consuming tasks in a fraction of the time it takes a human worker. This allows businesses to allocate their employees to other, more important areas. The result is a more efficient workflow that helps minimize direct labor cost. But how do you go about automating these tasks?
This is where inFlow steps in. Instead of sinking time into managing spreadsheets, inFlow consolidates information in one place and provides updates in real-time. It has the ability to create a bill of material (BOM), as well as help calculate your cost of goods sold. Gone is the need to monitor stock levels and calculate potential output– inFlow does it all instead.
0 Comments