Key takeaways
- Accurate inventory tracking involves batch, serial, and lot number tracking to ensure traceability from manufacturing to sale.
- Lot numbers identify groups of products produced simultaneously with the same materials and are common in industries such as food, pharmaceuticals, and automotive.
- Not only are lot numbers often required for regulatory purposes, but they also help facilitate targeted recalls, which reduces waste.
- Serial numbers uniquely identify individual units of a product and are essential for warranty services, tracking specific items, and aid in product recalls and service eligibility verification.
- Businesses should record lot and serial numbers upon receipt and during stock transfers.
- Barcodes can be used to streamline the identification of serial and lot numbers to minimize errors.
Accurately tracking inventory can require more than just stock counts. Many products have batch, serial, and lot number tracking; properly managing these is just as important as monitoring your inventory levels.
For example, lot and serial numbers can track components from the manufacturing level to the final product’s sale. This traceability is essential in certain industries like food and pharmaceuticals, but other sectors also benefit significantly by using serial and lot number tracking. In this post, we’ll dig through what each of these numbers represents and how you can effectively track them.
Are you more interested in a quick video overview instead? Well, you’re in luck! Watch this short clip from our new podcast.
What are batch and lot numbers?
The terms batch number, code number, and lot number are interchangeable, so we’ll use lot number for simplicity going forward. Lot numbers identify a group of products that were all produced simultaneously using the same batch of ingredients or raw materials. You’ll find lot numbers commonly used in the food, automotive, and pharmaceutical industries. They can also help track children’s products.
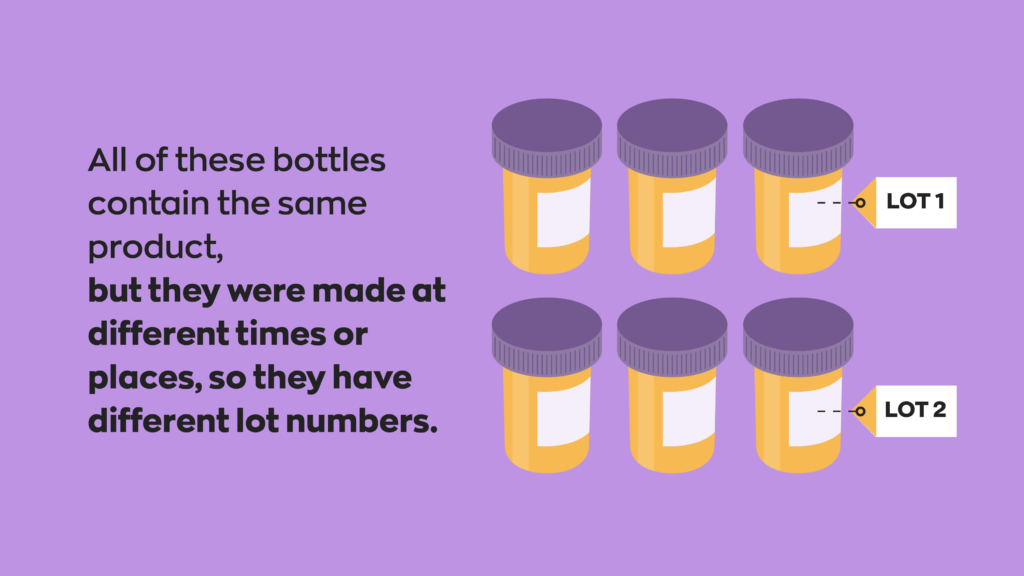
Lot number tracking can save manufacturers a lot of money and effort. If a product has a problem, you can recall specific lot numbers. For example, a pharmaceutical company discovers a dangerous ingredient in one of its drugs. Rather than dispose of everything on their shelves, they can use lot number tracking to target a recall of the affected products.
Are you having an issue with a product? You’ll likely report it to a manufacturer using lot number tracking. Sometimes, manufacturers give lot numbers a prefix (e.g., Lot 114321). Other times, they might stamp or print them on the product.
What are the benefits of lot number tracking?
Some of the most common reasons a manufacturer may want to track lot numbers are:
- Comply with regulatory standards: If you manufacture perishables, food products, or pharmaceuticals, lot number tracking may be a legal requirement.
- Improve customer satisfaction: Lot number tracking means you can more quickly identify and respond to any potentially defective, damaged, or dangerous products.
- Reduce waste: When you issue a recall, you can pinpoint specific batches of products, eliminating the need to purge everything you have on hand. This can drastically improve your margins.
- Better product forecasting: By using data in lot numbers, such as when you produce certain items and how many are available, you can create accurate customer demand forecasts.
- Clear communication: Utilizing lot number tracking will ensure everyone across all departments has a clear line of sight into the production process.
Lot tracking best practices
No matter what system you use for your serial and lot number tracking, there are some best practices to remember.
For example, fulfilling orders based on specific lot numbers will ensure accurate monitoring and help prevent mix-ups. Incorporating a barcode system will streamline the lot number tracking process, allowing for quick and precise identification and recording. And finally, implementing software that can help with your serial and lot number tracking will go a long way to keeping things recorded and tracked correctly.
How do I start lot number tracking my products?
If you purchase products that have lot or batch numbers, record them as you receive them on each purchase order. Specifically, record how many units you receive and the lot number assigned to them. You’ll then want to store all units with the same lot number in a single space for easy tracking.
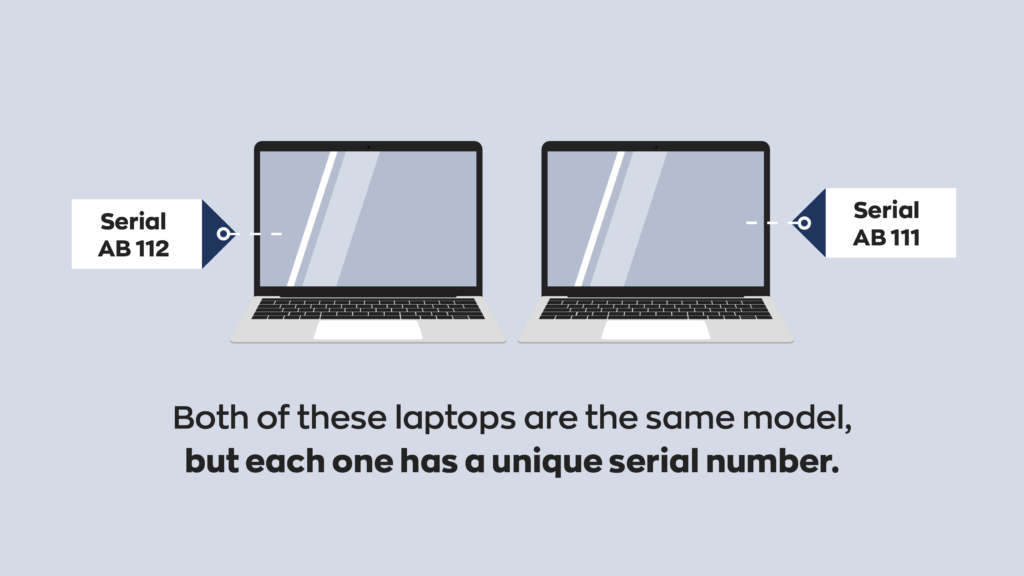
It’s most convenient if your inventory system can record a lot number directly. If there isn’t a dedicated space for recording one, you can also record the lot number as a sublocation. For example, if you’re storing a particular lot in Warehouse A, you can log its location as Warehouse A, Lot 345.
Including the lot number on your invoices to customers may be optional. But you will want to track it on the pick list for each invoice. That way, if your customers process any returns due to defects, the pick list will help you quickly identify the lot number in question.
[inFlow Cloud tracks lot numbers using the sublocation field. For more details, see this sublocation article.]
What is a serial number?
While lot numbers refer to a group of identical products, serial numbers help to identify individual units of a product. In other words, they’re even more specific than batch or lot numbers. Manufacturers could give the same lot number to tens, hundreds, or even thousands of identical products. On the other hand, you would only assign one serial number per unit. In other words, serial numbers make products unique, so you can differentiate one unit from another.
If you look at the bottom of a laptop, you’ll likely find a serial number printed or engraved on it. If you don’t see it there, the number is often associated with your purchasing account. The retailer will print the serial number on the original invoice in this case.
You can use serial numbers for recalls, but they’re also handy for service eligibility. For example, warranty and repair services often require you to provide the manufacturer with a serial number. Additionally, invoices that include the serial number will help identify the date of purchase.
Serial numbers can also contain more information about the product. The encoding can vary from company to company, but you can commonly use a product’s serial number to identify its model number, date of manufacture, and even manufacture location.
How do I track my serial numbers?
If you sell serialized products, you’ll need an extra level of precision in your inventory tracking. When you receive your products, you’ll have to record how many units you received, as well as the serial number assigned to each individual unit.
Record this serial number on any stock transfers to other storage locations and any sales or returns. Entering long serial numbers after every product movement can be time-consuming. For this reason, having your serial numbers printed out as scannable barcodes can be helpful. This way, your staff can use a barcode scanner to scan how much of a particular product they moved. Then, scan a second set of barcodes to identify precisely which serials were included in that transaction.
We’ve heard from customers that they previously tracked serial numbers using complex spreadsheets. Each row of these spreadsheets would represent a product and its corresponding serial number. While these can work for smaller batches of serialized products, it can also be very easy to make mistakes and overwrite data.
We’ve designed inFlow Inventory to make this process easier. inFlow ensures that serial numbers follow serialized products through every stock transfer and transaction — from initial purchase to final sale. So you can rest easy knowing that you can track your serial numbers without resorting to giant spreadsheets to manage them. Not to mention our barcoding
If you’d like to simplify serial number tracking, inFlow Inventory can help!
The article is nice but does not tell me how to do that in Inflow. This is what I need to track inventory with a lot number then stored by shipper 1 2 3 4 5 with multiple serialized units 32 34 35 ….
Hi Sophie!
good question. inFlow doesn’t have a field called named lot numbers, but we do have sublocations: https://www.inflowstaging.com/support/cloud/how-do-i-track-lot-numbersbatch-numbersexpiration-dates/
Those sublocations could then be named after shippers or lot numbers.
Within each sublocation, you can store serialized products as long as you’re using our Advanced/Enterprise plan on Cloud: https://www.inflowstaging.com/support/cloud/can-i-track-products-with-serial-numbers-using-inflow/
So as a final example, you could have a Location (Warehouse A), Sublocation (Lot 45), and have products in that lot also support unique serial numbers.
I hope that helps, and our support team would be happy to help with any other questions that might pop up. The easiest place to find them is here: https://www.inflowstaging.com/software-contact-info
I’d like to know a bit more about this product? Can you use warehouses as a different feature to say equipment is in storeroom, has been moved to staging and now it’s couriered to customer and finally closed Inventory?
I’m trying to find something that can help with managing the tracking stages of customer equipment from when it is delivered to us through the stages and then received/closed by customer. Ideally I would require fields that are associated to PO or/and SO’s. Part number, serial number, customer name etc.
Hi Robyn,
Thanks for getting in touch!
The quick answer is that inFlow can handle workflows where you just need to keep track of local inventory, and it can also help you record the process of sending products to customers and properly removing them from inventory. The thing we do not currently track is when the products are received by the customers; currently they would have to tell you that themselves or you’d have to check based on tracking numbers.
Since you left your email address with us, I’ve forwarded your questions to our support team and they’ll be in touch via email with followup!
What is this the serial number of?
JxNRCV200703117
Sorry Caleb, serial numbers are pretty specialized with prefixes and suffixes, so without having more context like the manufacturer and type of product, it’s not usually possible to tell from the serial number alone what product it would belong to. Sorry we can’t help more here!
How can I trace a serial number to a camcorder to see if it was stolen
Hi Renee,
If it was a camera sold at your store, then you’d be able to investigate and see if that serial number was ever on any sales orders (if it wasn’t, then it may have been stolen).
hi! is it possible to create a lot number with serial number? if possible, how? for breads and cakes having 2 or more commissary. hope to here from you the soonest. thank you!
Hi Averie,
Our software doesn’t currently explicitly support lot numbers, but we do offer a workaround where you use a sublocation to represent lot numbers.
So you could create a serialized product in inFlow and then store it in a sublocation that reflects its lot number.
We manufacture architectural stone veneer.
We sell the stone “per square foot”. But it’s packaged on individual pallets. One pallet might have 150 sq ft…..the next pallet might be 200 sq ft of same stone. All inventory eventually leaves the warehouse on a pallet.At any given time there might be 100 pallets of stone in the warehouse with different quantities of stone…
My question: Would giving each pallet a serialized number be my best option?
Hi Tommy, yes, serializing each pallet could work. We also support prefixes for serial numbers, so you could have different prefixes to denote different sizes of pallet.
The other way to work around this would be to make a sublocation out of each pallet and receive pallets to their own unique sublocations.
We are just starting our business of manufacturing of metal parts, wherein we have to record the certificates of each metal used. I am having trouble giving a unique identifier to the Lot Number to be used to trace the parts made from the metal supplied from each supplier. Could the lot number be the same as the Sales Order from the supplier only with “LTN” in front of it, and the part number of the product following, with the storage location following that, as example (Warehouse ) WH1. Then when a part is made from this metal, should that lot number be on our sales order to the customer? Having a problem (in my head ) as to how to marry up all the numbers ( SO, PO, WO and Lot number ) and easily trace them all back to the original order. Thank you for your input!
Hi Jan,
Hrmm, this might be better as a support ticket with our team, but I’ll give it a quick try in comments.
Assuming you’re using inFlow, if you’re trying to keep a consistent lot number, you could try using a sublocation to represent the lot numbers and the locations to represent the warehouse as a whole. If your supplier doesn’t provide a lot number, I think your idea of basing it on a PO or SO number works, since those must be unique in inFlow (no duplicates).
So if you bought metal from a supplier on PO-0001 and you stored it in WH1, the location would be WH1 and the sublocation would be called PO-0001.
When you use that metal on a work order in inFlow, the Pick tab in your work order would serve as a permanent record of which lots were sourced in the work order.
The Put Away tab of the work order could also use that same PO-0001 sublocation.
This would mean that raw materials and finished materials would both occupy that PO-0001 sublocation, but if the items have very different names and descriptions, that could be OK.
The idea would be that the location represents the raw materials from that lot number, and final products made from that lot.
When you sell that metal, you’d pick from the PO-0001 sublocation and that would also be permanently recorded in inFlow.
If you needed to, you could print out the pick list and crop it to show the customer where those products were taken from. That would basically show the lots to them. It wouldn’t be on the invoice, but it could be a document accompanying the invoice — all generated by inFlow.
I hope that helps with some direction. If you have other questions, you can reach us through our support channels (support@inflowinventory.com) and live chat on http://www.inflowstaging.com.
– Thomas
You describe LOT numbers, but without a single information on where to find it in the Dear system. And I cannot find it in the system neither, why? Because it doesn’t exist. You are describing a feature (that is like a basic feature for inventory management) and then you only add an sentence “inflow doesn’t offer it, but a workaround”. Such a waste of my time, both for reading this article and for trying inflow.
Sorry we disappointed you, Grzegorz. This article is mostly about how people go about tracking lot and serial numbers—a kind of general overview. But we do mention that inFlow can help with these use cases, too. (We don’t mention Dear Systems because that’s not our software.)
However, since we wrote this article a few years ago we have added new features that improve lot number tracking within inFlow.
It was a workaround before, but you can now use sublocations in inFlow to represent lot numbers. There’s a setting in Cloud to help you automatically pick products based on lot numbers. If you’d like any help trying out this feature, please get in touch with support@inflowinventory.com and we’d be happy to assist.