Inventory shortages can affect a company’s profits directly and indirectly. Not having materials for production or products to fill orders leads to lost business in the short term. Shortages also affect long-term revenue because clients or retail customers may eventually move to competitors if you lack the products they want or need.
In some instances, companies have poor tracking methods and might not actually know their current supply levels. They may be selling products that are already out of stock or planning production runs without enough materials.
The solution to inventory issues is to carefully track materials and products so that you always have necessary products at hand without being oversupplied. The first step in managing your warehouses is to perform an inventory audit.
Inventory audits can be tedious and time-consuming, but techniques and cutting-edge software can reduce the burden while providing you with the necessary insights to improve your operation.
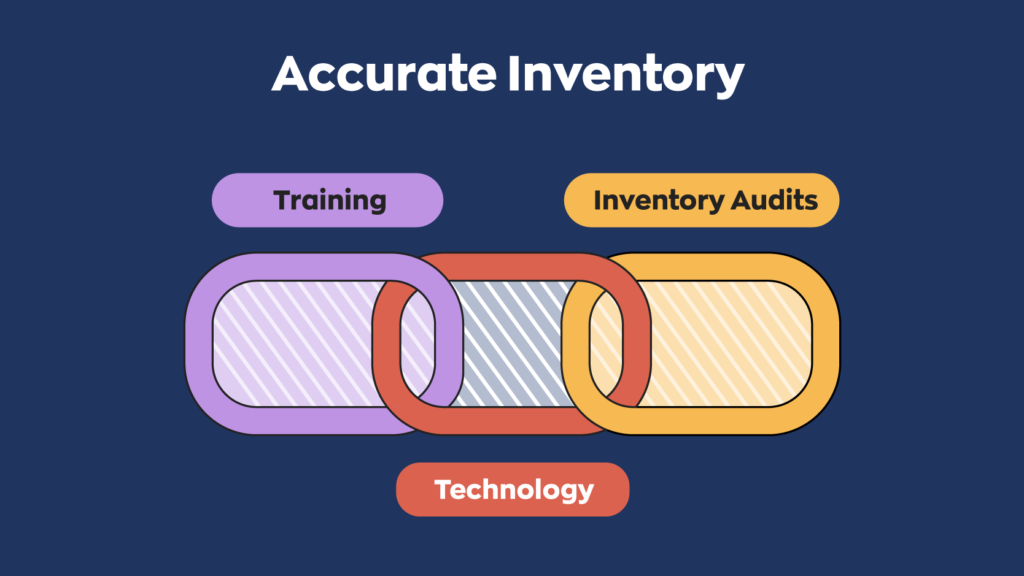
What is an inventory audit?
An inventory audit involves ensuring financial and business records match the actual stock in your warehouses, factories, or shops.
In some cases, this process can be as simple as manually counting products and seeing if the sums match the totals in your accounting software. In some cases, internal auditors can handle the process, but a company can also hire a third party to assess its warehouse system.
The goal is to ensure inventory is at appropriate levels and the current process of tracking and recording stock is effective and accurate.
Inventory audits often go beyond counting products. They may also include the condition and location of the products and how each is represented in company records.
Auditors may also outline problems in the inventory counting process, such as delays between intake or shipping and entry into the inventory or accounting systems.
When are inventory audits required?
Publicly traded companies need a third-party inventory audit annually to comply with regulations. The auditor needs to be accredited, independent, and not affiliated with the company. The goal of this assessment is to verify that inventory levels and values are accurate on the firm’s financial reports.
Though not required by law, private companies may perform inventory audits annually. They assess the effectiveness of their systems and tracking processes and look for issues and opportunities to streamline warehouse management practices.
Depending on the size and complexity of the company, the audit may take several days or weeks to complete. Inventory assessments can coincide with broader financial audits.
What constitutes material inventory?
Products and supplies are material inventory if they can individually or collectively influence the economic decisions of a company. In other words, all the things necessary for a company to manufacture products or provide services are considered material inventory. Finished products or components also fall into this category.
Unfortunately, there is no standard definition of material inventory. Auditors rely on a set of criteria to determine if products are material.
One of the following must be true for material inventory.
- It must account for at least 0.5–1% of sales revenue;
- 1–2% of total assets;
- 1–2% of gross profit;
- 2–5% of shareholders’ equity;
- Or 5–10% of net pre-tax income.
Any inventory above the mentioned ranges is automatically material. The auditor uses their discretion for products falling within the ranges.
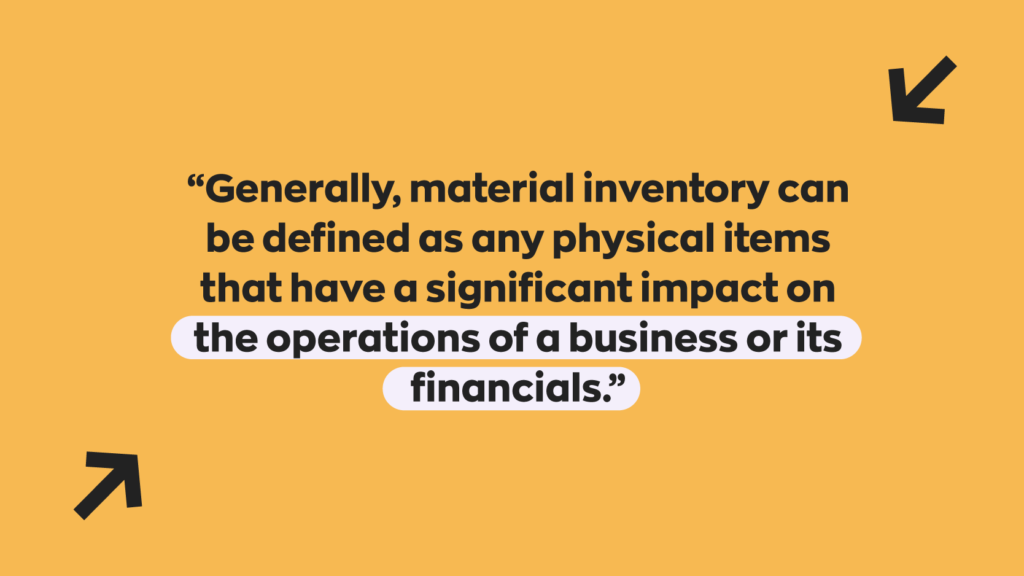
Auditors can use additional criteria, as well. For example, material inventory can be individual high-value products, products that are difficult to replace, and equipment essential to company operations.
What are the benefits of inventory auditing?
Any company can benefit from inventory auditing. Here’s a look at some of the advantages for both public and private companies.
Calculate profits
Inventory audits can help businesses compute their profits more accurately by providing an account of their current inventory levels and relevant transactions.
These insights are beneficial because they help businesses accurately define trends that help forecast their sales and profits. With these predictions, they can assess current inventory to ensure they are not over or under-supplied.
Create more accurate budgets
Inventory audits also provide businesses with insights into current stock levels and how they relate to market trends and demand. This information helps plan more accurate budgets for stock ordering, warehousing, and customer order fulfillment.
By keeping stock of the available inventory levels, businesses can plan and time supply levels and avoid over-ordering and wasting resources. They can also ensure they always have sufficient supplies to meet demand and limit shortages.
Identify inefficiencies in your operations
Auditing can help businesses identify inefficiencies in their warehouse management methods by providing an objective assessment. Auditors can review processes and procedures to determine inefficiencies and identify possible improvements.
Auditors can also identify inaccurate or unsecured tracking techniques, helping businesses avoid losses before they occur.
Reduce carrying costs
Carrying costs are expenses associated with storing, transporting, and managing inventory. These expenses will typically cover storage, insurance, and taxes. Inventory auditing can help businesses identify ways to reduce carrying costs by ensuring that proper inventory management processes are in place.
What analysis methods are used in inventory auditing?
Auditors can use different analysis methods. The most accurate approach will vary depending on the industry and individual needs of a company.
Here is a look at the six most common methods auditors rely on when assessing a business’s inventory.
- Cutoff analysis: This method involves halting receiving and shipping operations while physically counting available inventory. The stoppage ensures better accuracy. This approach is best suited for businesses with a large number of products, as it can help identify potential discrepancies in the supply chain.
- Physical counts: This method involves manually counting the physical products in the inventory and comparing the totals to the figures in the accounting system. The approach is most suitable for businesses with expansive inventories, because it can help to identify discrepancies between physical products and records.
- ABC analysis: The ABC analysis method classifies products into three categories — A, B, and C — based on their importance or value. Things in the A category are the most valuable, B products are moderately important, and C materials are the least essential. This method is best suited for businesses needing to prioritize warehouse and ordering around specific products or supplies.
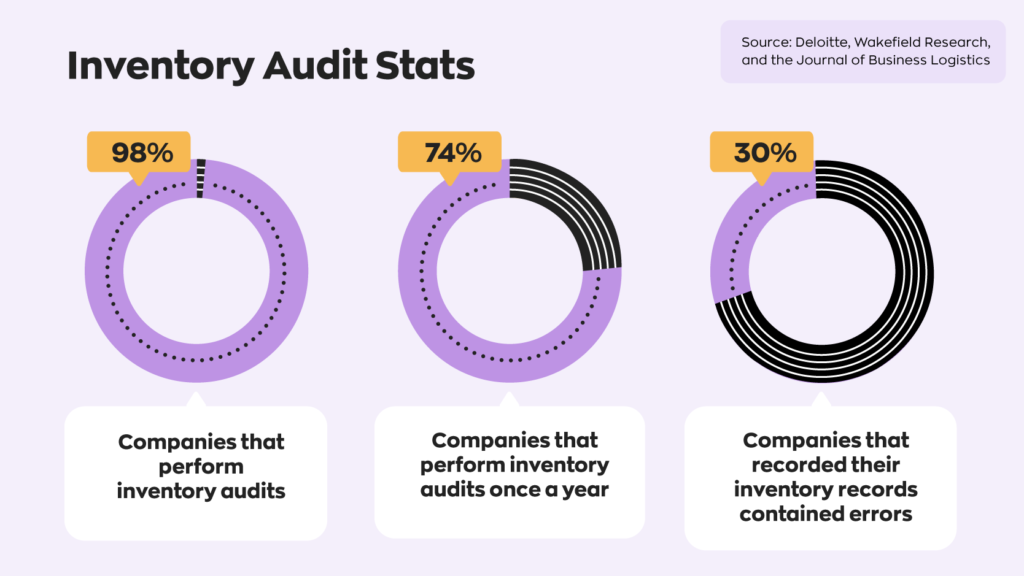
- Finished goods cost analysis: This method involves reviewing the costs of producing finished goods to assess the completeness and accuracy of overall cost records. The strategy is best for manufacturing businesses because it can help to identify potential issues with the production process or cost structure.
- Freight cost analysis: Freight cost analysis involves reviewing shipping and receiving costs. It assesses factors such as the price of shipping, the time in transit, and any potential damages that may occur to the inventory during transport. It is best suited for businesses that ship and receive many products, and it can identify potential cost savings opportunities.
- Overhead analysis: This audit method analyzes the costs associated with overhead, such as rent, utilities, and insurance. These expenses often affect the overall cost of inventory management. Companies with a lot of warehouse space or insurance costs can gain insights from this auditing approach.
An auditor might combine more than one method to provide the company with the desired insights.
Planning an optimal inventory audit
Inventory audits are only valuable if they provide the correct insights. Poorly timed audits that don’t use the proper documentation or information will not be useful to a company.
Here are steps to ensure your inventory audits provide the necessary insights.
Pick the right time
Auditing often requires stopping operations. Since audits can take multiple days, you do not want to schedule them during a busy time. For example, an ecommerce site or retail company would not want to pause its warehouse operations during the holiday shopping season.
You can schedule audits during your company’s slow season or after production runs. At the same time, you want enough stock on your shelves to ensure an accurate and insightful audit.
Prepare your inventory
You can make the audit process more efficient by making products easier to count. For example, a company might store products in similar categories together or combine them into uniform groups so that auditors can count the group as a whole instead of individual products.
You can also map out your warehouse and organize products by category (such as shelf or pallet) using inventory and warehouse management software. These tools help auditors know where everything is so that they can count more efficiently.
Gather pertinent documentation
In addition to accounting records, auditors will use other documentation to assess the overall inventory tracking system. They might check invoices, shipping or receiving records and ordering histories.
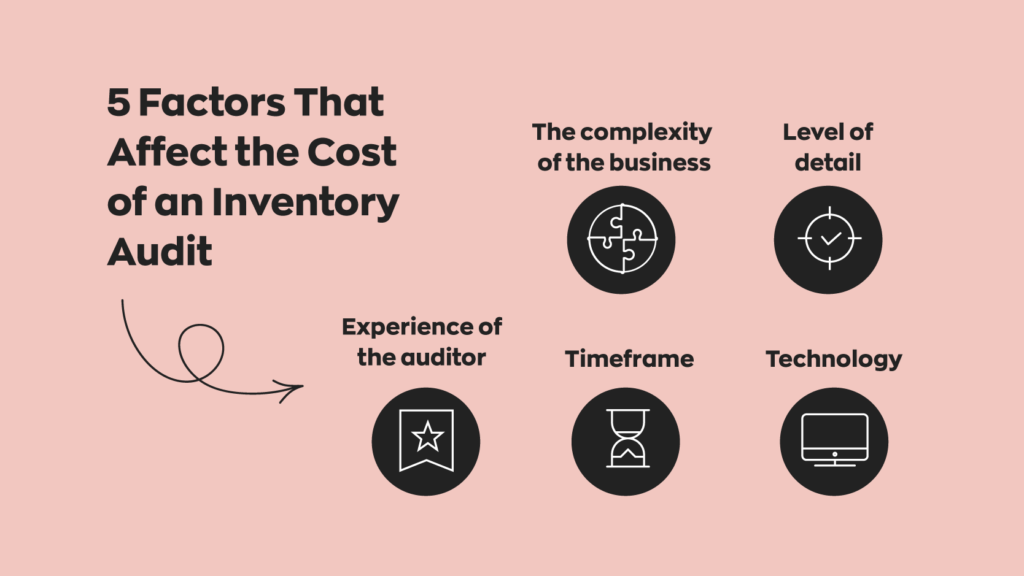
A company can generate these documents immediately if they use inventory management software for sales and invoicing or purchase orders. The data from this software can be used to generate reports giving auditors a look at the company’s overall inventory management.
Brief your staff
Staff members need to be aware of the audit and make any necessary preparations. Auditors may ask team members to assist with specific aspects of the counting or produce certain documents. Staff members need to understand their roles so that they can provide accurate counts or proper figures for the auditing process.
Utilize technology when you can
Inventory management software helps automate or streamline certain aspects of the process. For example, an accurate barcoding system streamlines counting and ensures more accurate records by reducing the potential for human error.
Inventory software reduces errors during daily operations, so it proves useful during non-auditing periods, as well.
0 Comments