Brick-and-mortar stores aren’t a relic of the past yet, but it’s safe to say that most people do the bulk of their shopping online these days. From the customer’s perspective, online purchases feel smooth and straightforward, but behind the scenes is a logistical whirlwind responsible for getting the products to your doorstep. One thing that warehouses, both big and small, rely on to streamline the fulfillment process is warehouse slotting.
Someone must pick a product, pack it up, and then ship it out. It’s a simple process, but it usually takes place in a massive warehouse that stores many different products. As a result, it’s essential to optimize the packing process, saving time and money in the process. One of these optimizations is warehouse slotting.
So, what is slotting? How does it help businesses save time and money? Let’s find out.
What is slotting?
Warehouse slotting means organizing the products in your warehouse in a manner that streamlines the fulfillment process. It’s simple on the surface but surprisingly complex once you really start to break it down.
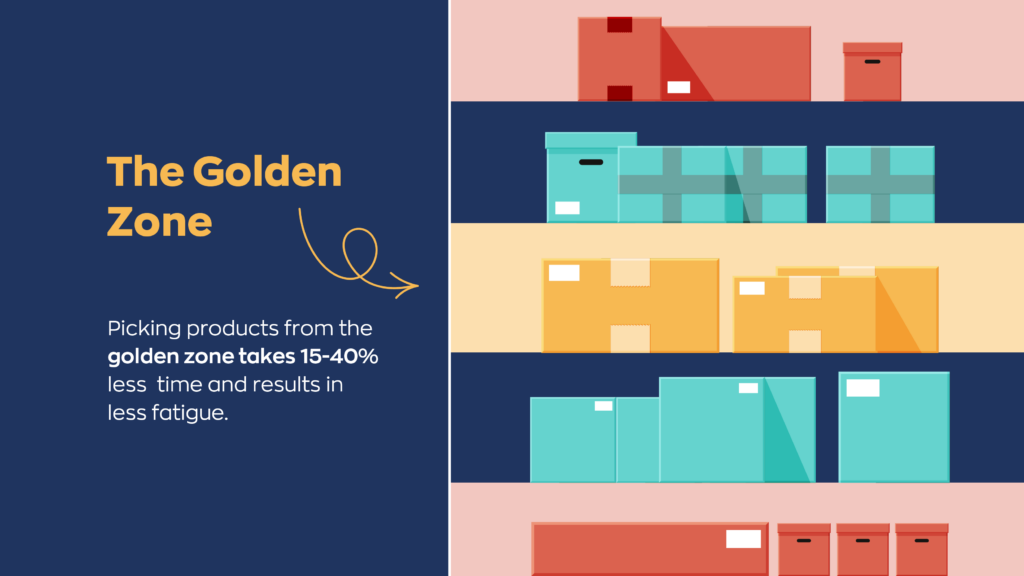
You can organize your slotting in several ways, such as product type, size, SKU, turnover ratio, or other relevant information.
Why do businesses implement warehouse slotting?
In short, it helps businesses get more out of their time and money. It does so in a handful of different ways, though, so here’s a quick breakdown.
Much greater efficiency
We already touched on the fulfillment process above. When an order comes in, an employee at a physical location picks the items, packs them up, and then ships them out. This is a time-consuming process, and it also comes with an opportunity cost. The time an employee spends on one order is time that they can’t spend working on another one. You can remedy this by hiring more employees, but at a certain point, continually hiring new workers will become too expensive. This is where warehouse slotting comes in.
By organizing the warehouse to make products more accessible, employees can complete more orders in the same amount of time. This might not mean much on an individual scale, but it adds up quickly over time.
For example, let’s say you implement a new slotting system where you place your two most frequently purchased items next to each other in the warehouse. This new system allows your order pickers to shave one minute off every order. On average, each of your warehouse pickers fulfills sixty orders a day. This would mean over the course of a day, each of your employees will have saved an entire hour of work.
Better accuracy
At its core, slotting is an organizational system. And having an organization system in place makes it easier to find things and cuts down on incorrect orders. If employees know where something is going to be at all times, all they have to do is walk there and pick it up.
An intuitive slotting system means less back and forth, which will ultimately result in fewer manual errors.
More efficient storage
Implementing a proper slotting system also helps fit more products into the same space. This, in turn, allows for more sales and increases revenue. It also helps businesses save money by cutting down on warehouse space. The less you rent, the more you save.
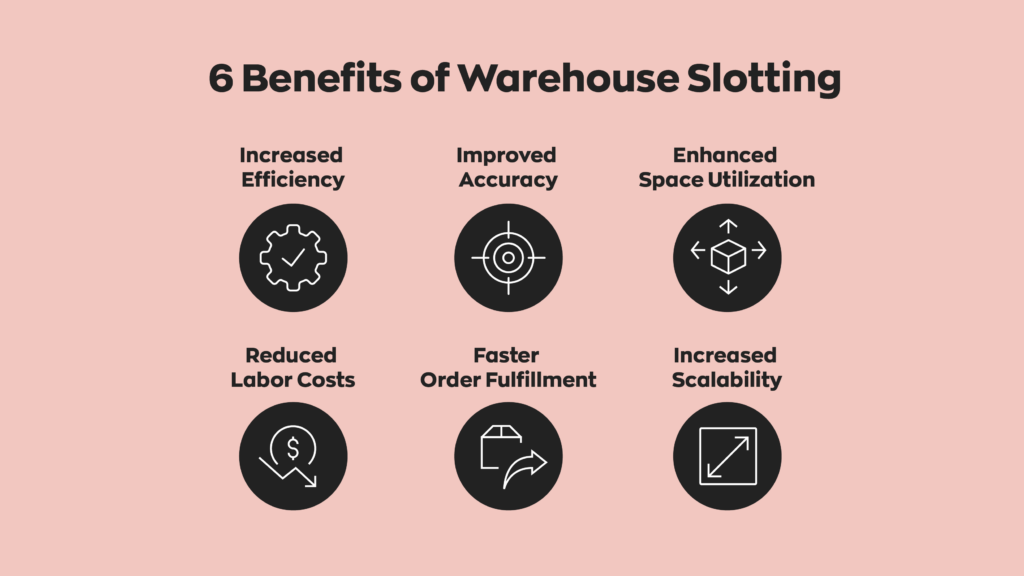
What should you consider when implementing warehouse slotting?
Slotting seems simple, right? Just put items with a high inventory turnover in easy-to-access areas and call it a day! In reality, it works out a bit differently. To truly optimize your slotting system, there are a lot of variables to consider.
The best place to start would be talking to your warehouse workers. They’ll be able to tell you firsthand what orders take them the longest to fulfill and why.
Many of our customers also use their reports in inFlow to gather valuable information that helps them set up their warehouse slotting. You can use this information to identify specific trends and variables, such as the following.
Bundle frequency
It’s a standard business practice to carry items that complement each other. This results in bigger sales, but in terms of slotting, it introduces some complications. Consider the following example. Product A sells more than Product B or C individually. But customers frequently buy Product B and C together, and their combined sales value is greater than Product A’s. In this case, it makes sense to skew slotting towards making Product B and C more accessible. It also makes sense to set up “zones” for commonly bundled items so employees can grab everything in one trip.
Product weight
Some products are light, and others are heavy. Others, still, are really heavy. Like need-a-forklift heavy. Moving products from higher shelves via forklift is an inherently time-consuming process. As a result, even if other products sell a bit better, it makes sense to put them closer to ground level.
Inventory turnover ratio
One of the most valuable variables you can use when setting up your warehouse slotting is inventory turnover ratio. Inventory turnover is how fast you sell through your inventory in a period of time.
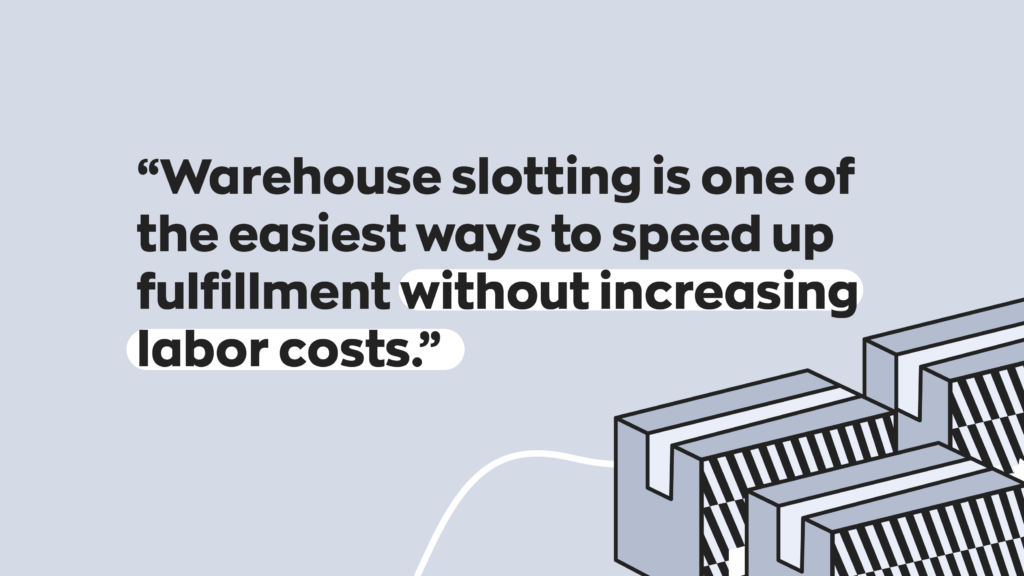
Typically, you will want to slot products with a high turnover ratio in a central, easily accessible area. At the same time, you could tuck away products with a low inventory turnover to harder-to-reach areas of the warehouse.
Downsides & pitfalls with warehouse slotting
Slotting is generally a boon to warehouse management, but as with anything, there are some downsides. There are also some common pitfalls to avoid if you’re looking at implementing your own warehouse slotting system.
Time-consuming implementation and maintenance
The inherent complexity of a slotting system means that it can be challenging to implement. It requires the careful collection and analysis of data over a long period of time. Additionally, rapid market changes can render systems obsolete quickly. Additionally, maintaining slotting can be a time-consuming process and, on fringe occasions, may outweigh the benefits.
Incoherent data
Implementing slotting requires a lot of data. How you collect and store your data will play a significant factor in how simple it will be to implement effective warehouse slotting. For instance, if you’re mainly using spreadsheets or manual methods of tracking your inventory, it will take a lot more time to collect and analyze your information.
Using a comprehensive platform like inFlow that integrates into every part of your business reduces the time spent compiling information. This makes effective warehouse slotting a breeze.
Perfection might not be possible
In theory, there’s a perfect slotting system that maximizes profit and minimizes overhead costs. In practice, though, that perfect solution might not be feasible. It’s best not to focus too much on the perfect solution and think of it more as the best solution. An ideal warehouse slotting system is all about creating balance.
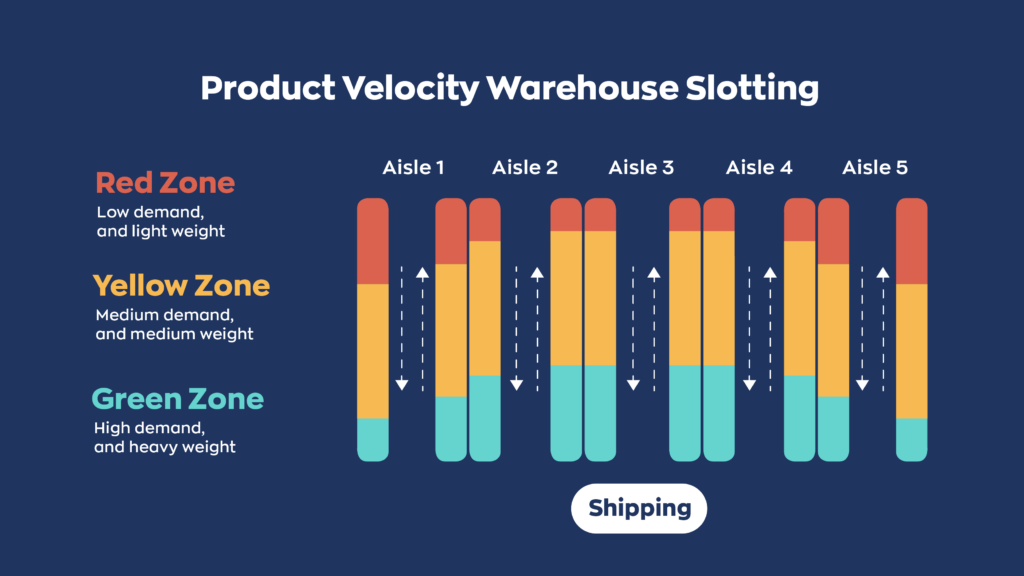
How inFlow can help your warehouse management
Implementing slotting can go a long way in optimizing your warehouse processes. But ultimately, it’s just one piece of a much larger puzzle. Running a smooth warehousing operation is all about using the proper tools, so we always recommend our software inFlow for anyone looking to take complete control of their business.
Thousands of businesses, big and small, love inFlow’s intuitive design. Our system is so easy to use you won’t need to hire a consultant to get it up and running. Our software offers real-time inventory tracking and allows you to pick, pack, and ship right from our mobile app.
Try inFlow today and see why we were rated #1 on Softwareworld’s list of top inventory management software!
0 Comments