How to create a bill of materials (Web)
A bill of materials is a list of raw materials and components that are used to manufacture a product. You can also track costs and manufacturing instructions. Take a look below to learn more.
Please note: Bill of materials is only available with an inFlow Manufacturing plan.
Bill of materials
The product record Manufacturing tab is where you can organize raw materials/components for a bill of materials. You can track the following:
- Components products
- Component product costs
- Operations
- Disassembly
Using inFlow for Windows? Take a look at this guide.
Creating a bill of materials
- Open a product, and select the Manufacturing tab.
- Click Add a bill of materials.
- Select the products from the product list. You can scan or click on the same product multiple times to increase the quantity of the component product. Click outside of the product list to close it.
- Click Save when done.
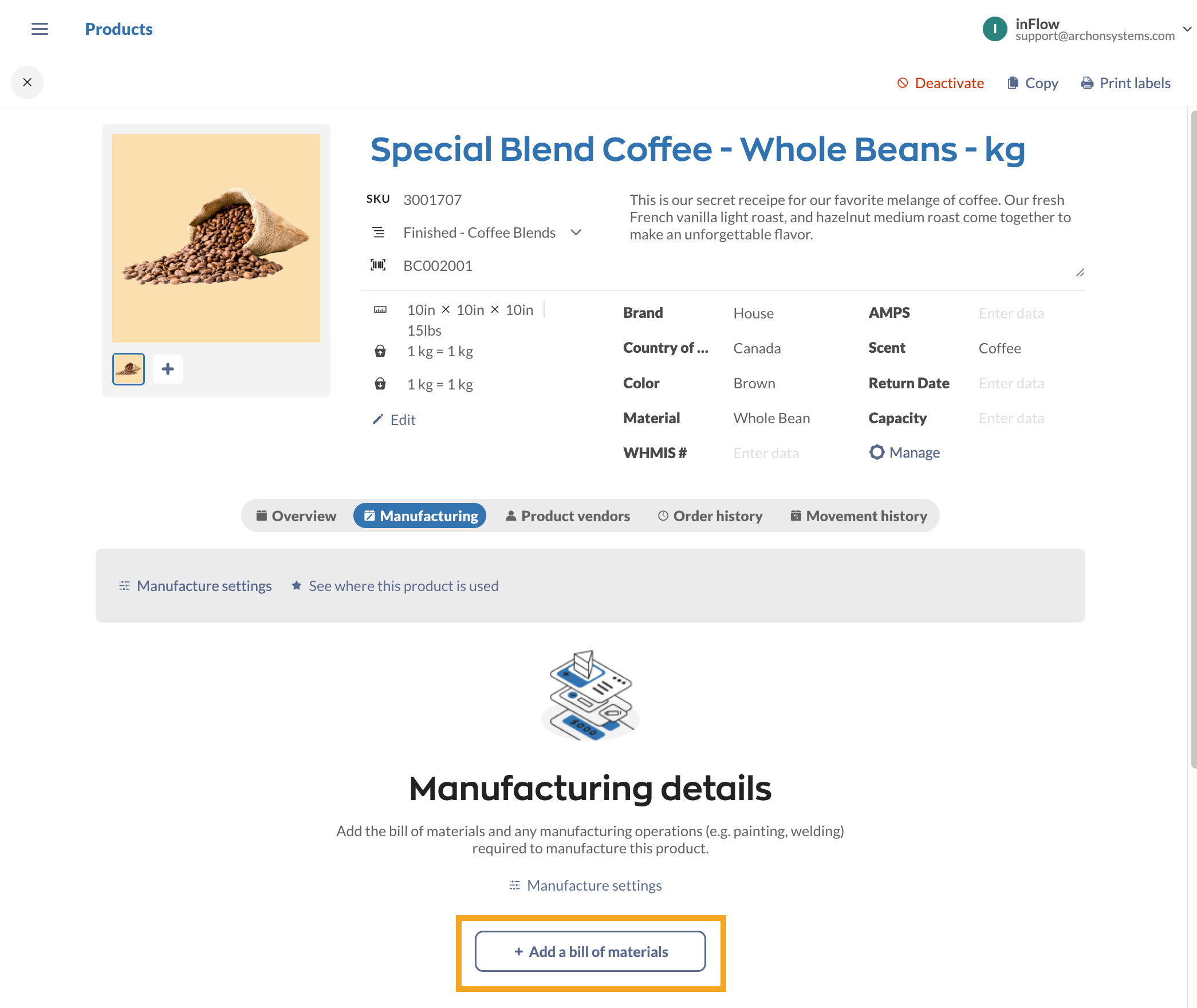
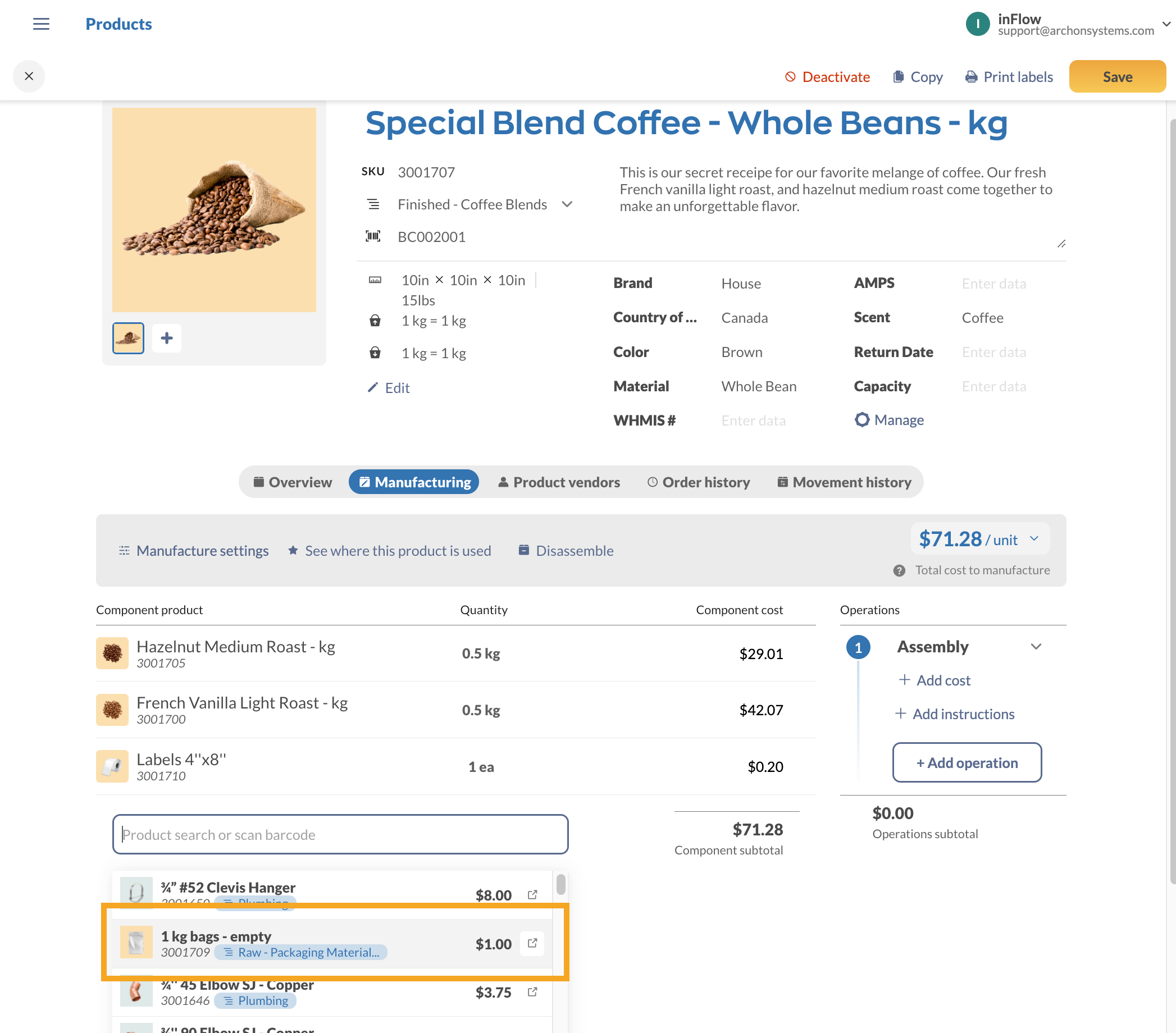
How can I add a bill of materials for multiple products?
If you have many products with a bill of materials, you can add them to inFlow in bulk with a CSV import. This article provides a full guide.
Customizing the bill of materials list
Sorting products
To sort out the products in the table, click on the headers that match the filter you want to apply.
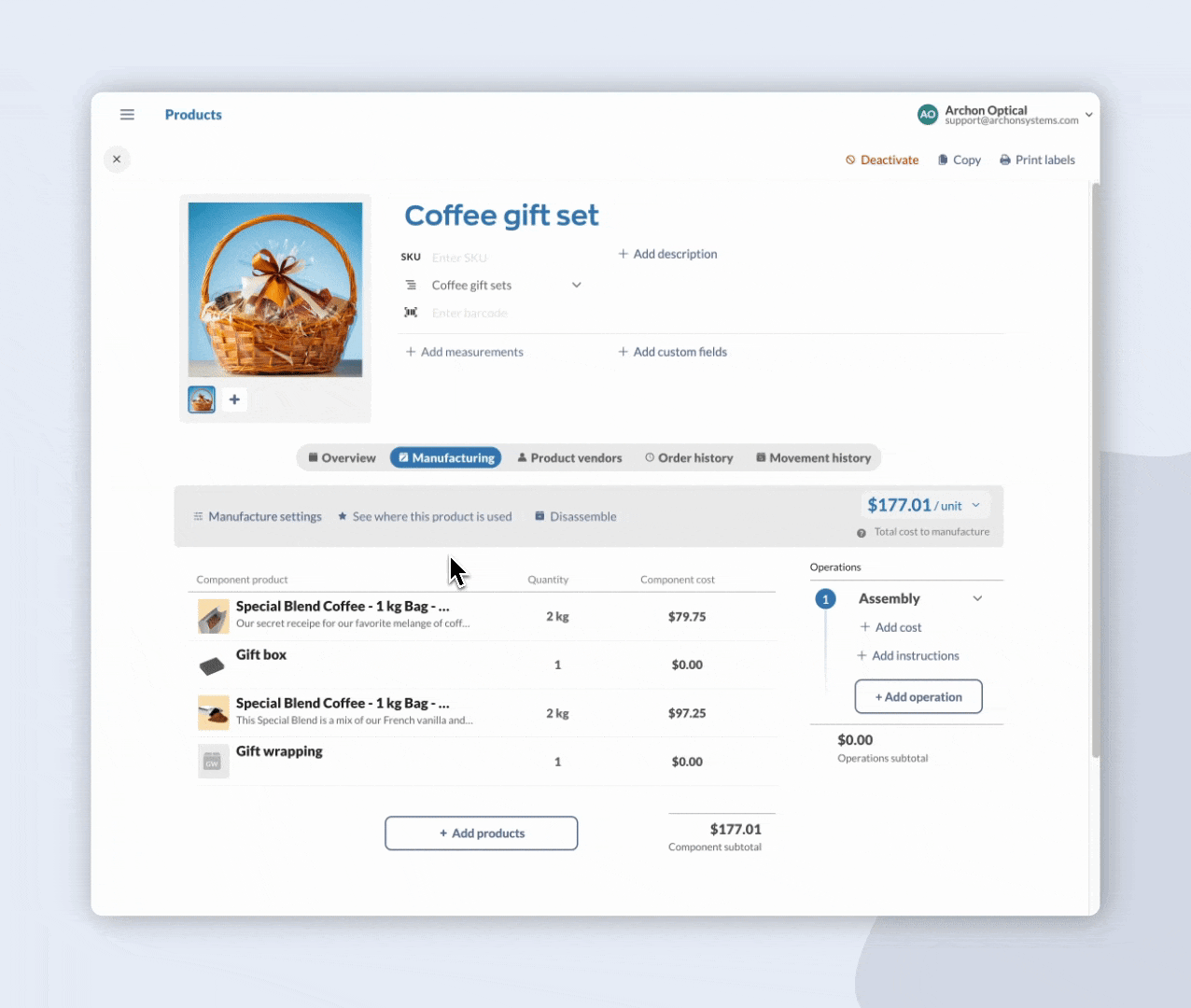
Rearranging products
Rearrange the products on the list by clicking and dragging the grab handles to the left of the product.
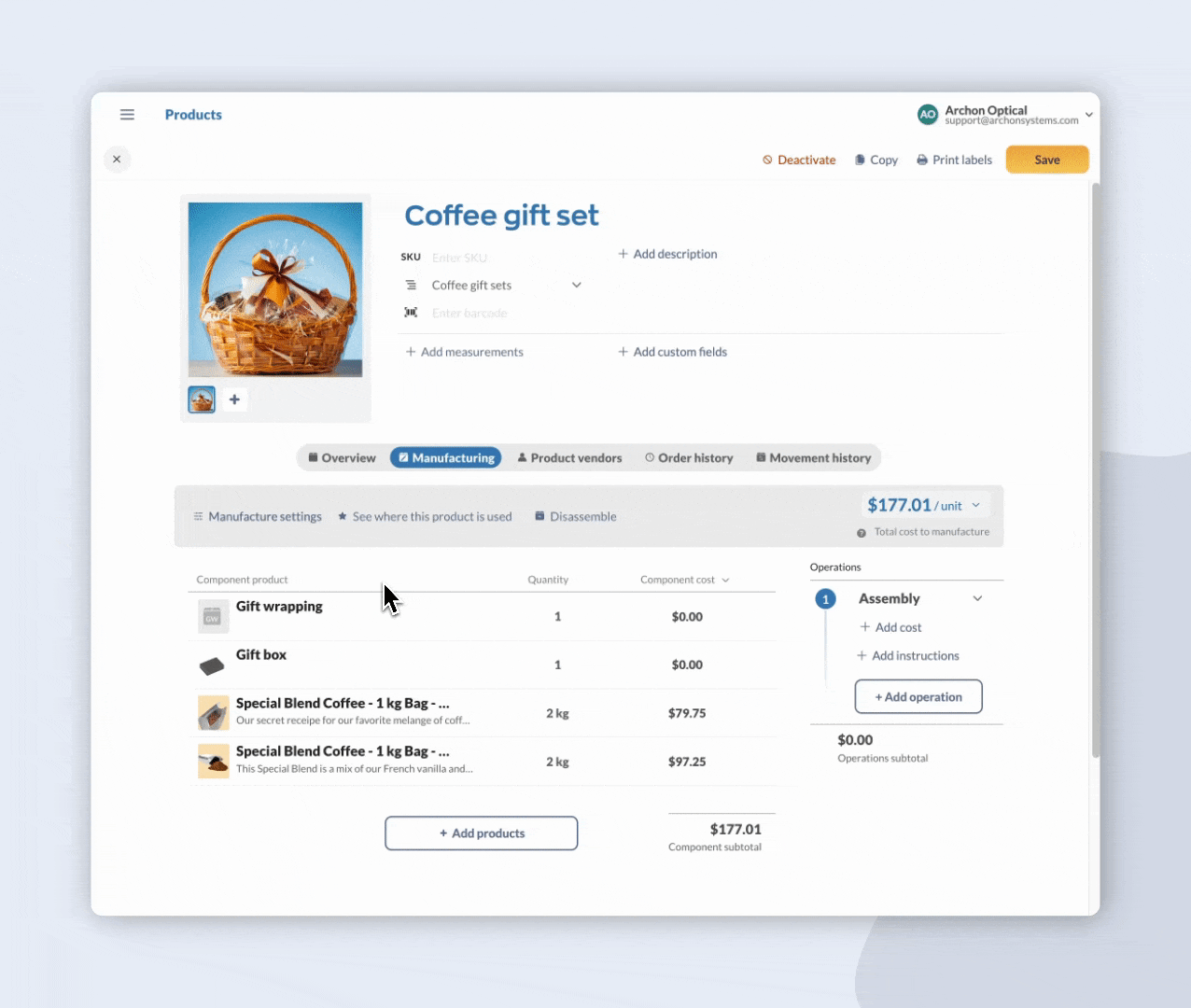
Viewing product records
If you want to look at a product that is on the bill of materials list, hover over it and click the link to open the product record in a new tab.
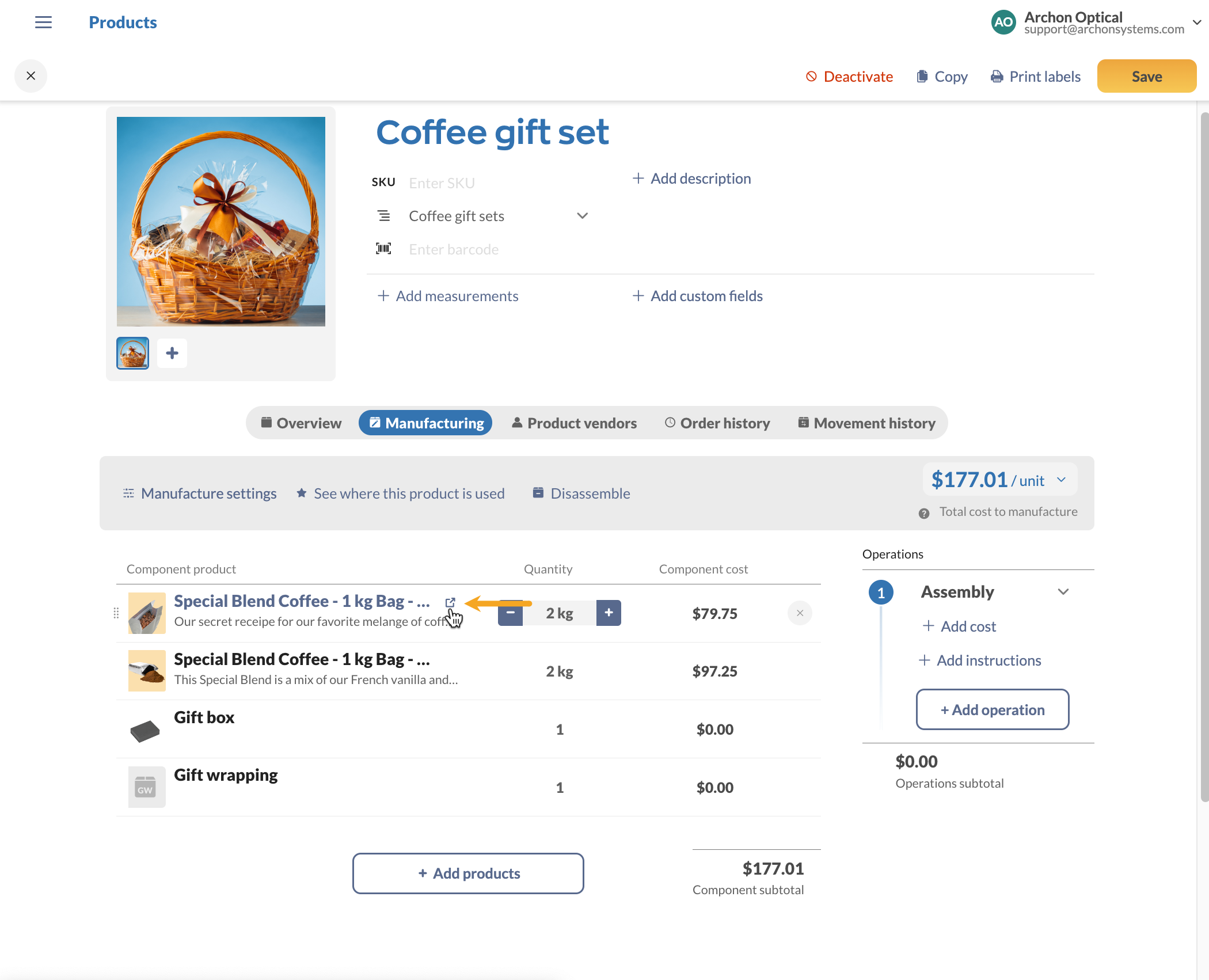
Removing products from a bill of materials
- Hover over the component product in the bill of materials list, and select the X to the right of the product to remove it.
- When done, click Save.
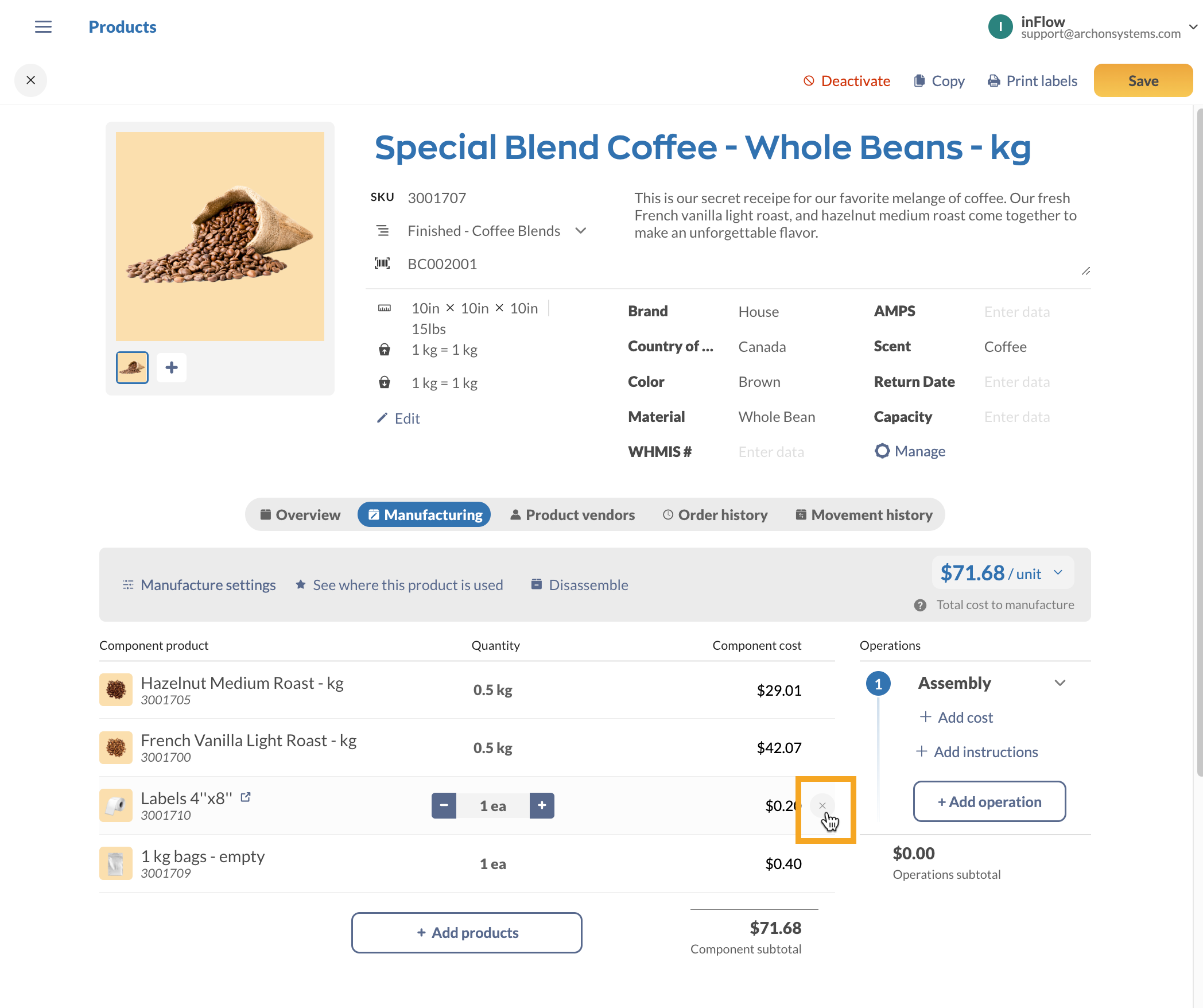
Costs
Cost tracking is vital in keeping your company on budget when it comes to manufacturing. The Manufacturing tab shows the total cost to manufacture for all products in inFlow with a bill of materials.
The Total cost to manufacture is a calculated estimate of how much one standard unit costs to make.
This estimate is based on component and operating costs from purchase orders and manufacturing cost fields throughout inFlow.
Cost formula
Cost to manufacture/unit = materials cost + operations cost
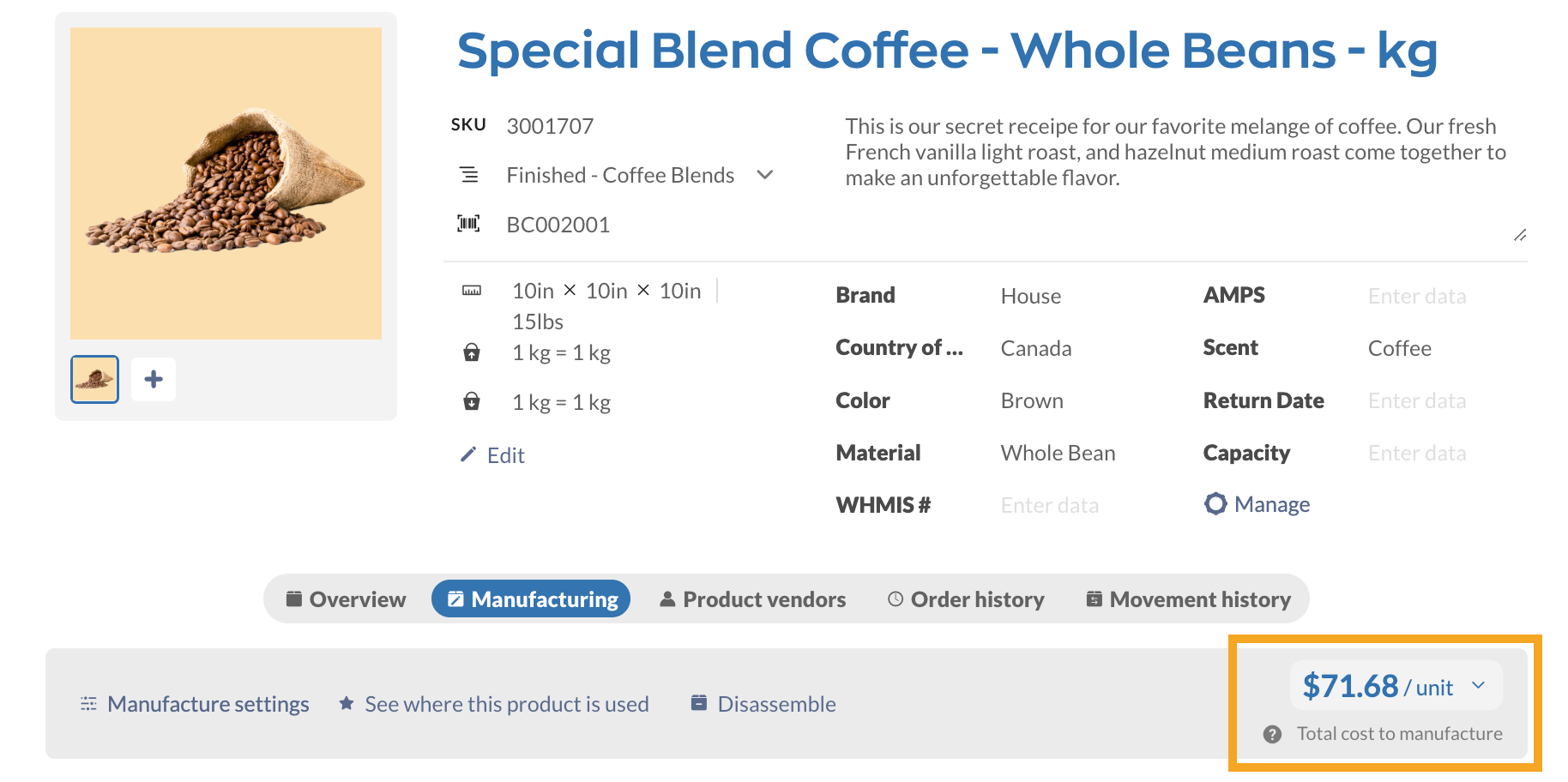
Total cost to manufacture breakdown
When you hover over the Cost to manufacture, you’ll see the Materials cost, Operations cost, and the total cost to manufacture.
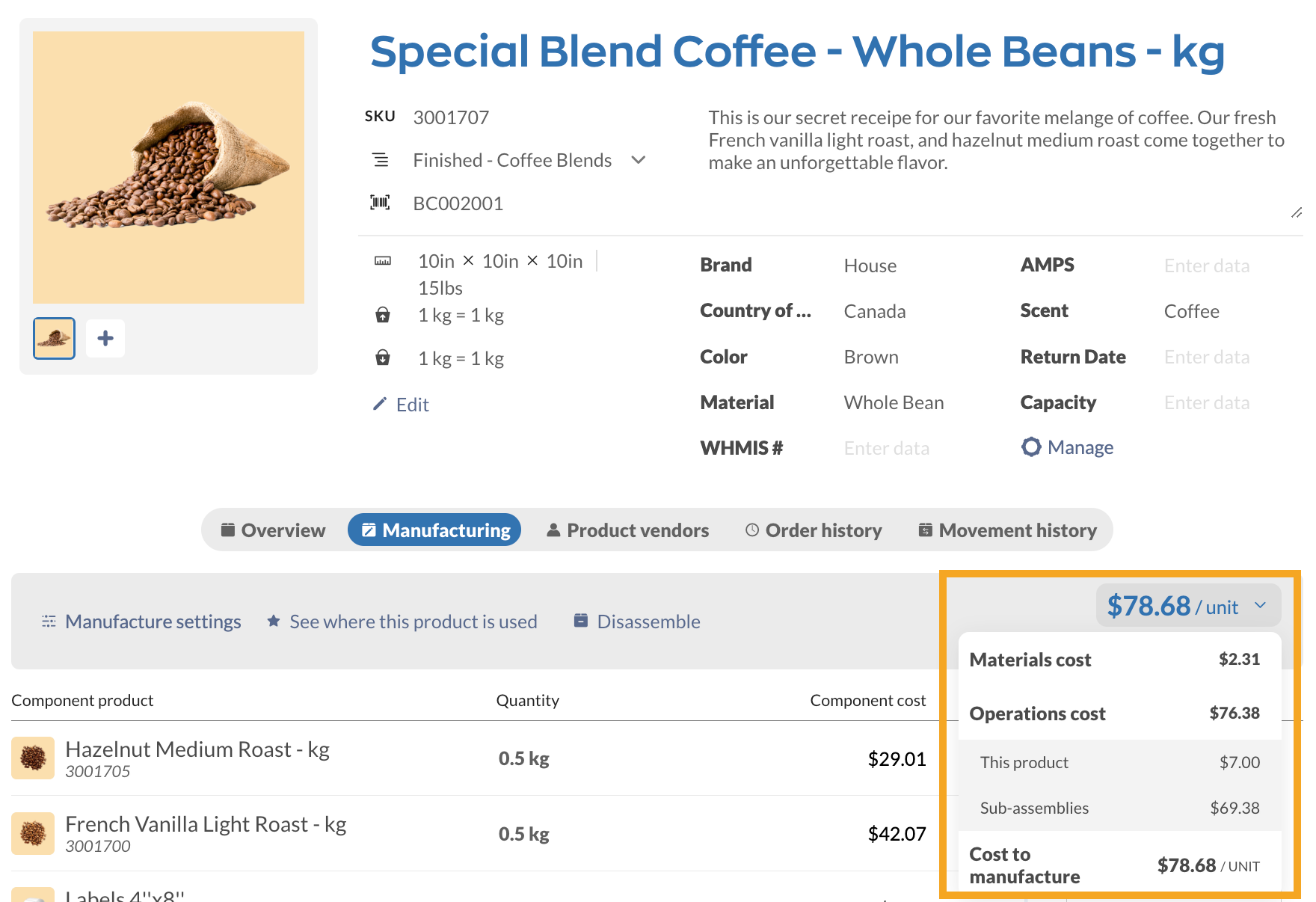
See the chart below for a better understanding of the Materials cost and Operations cost.
Cost type | Explanation |
Material cost | Cost of raw materials/components (excluding operating costs and labor). |
Operations cost | The total cost of all of the operations to manufacture one unit. Included are the operation costs of subassemblies that are completed to manufacture one standard unit. Per-unit costs and labor costs are part of the operation cost. |
Manufacturing Operations
Operations are where you can track instructions and related costs for each stage of the manufacturing process.
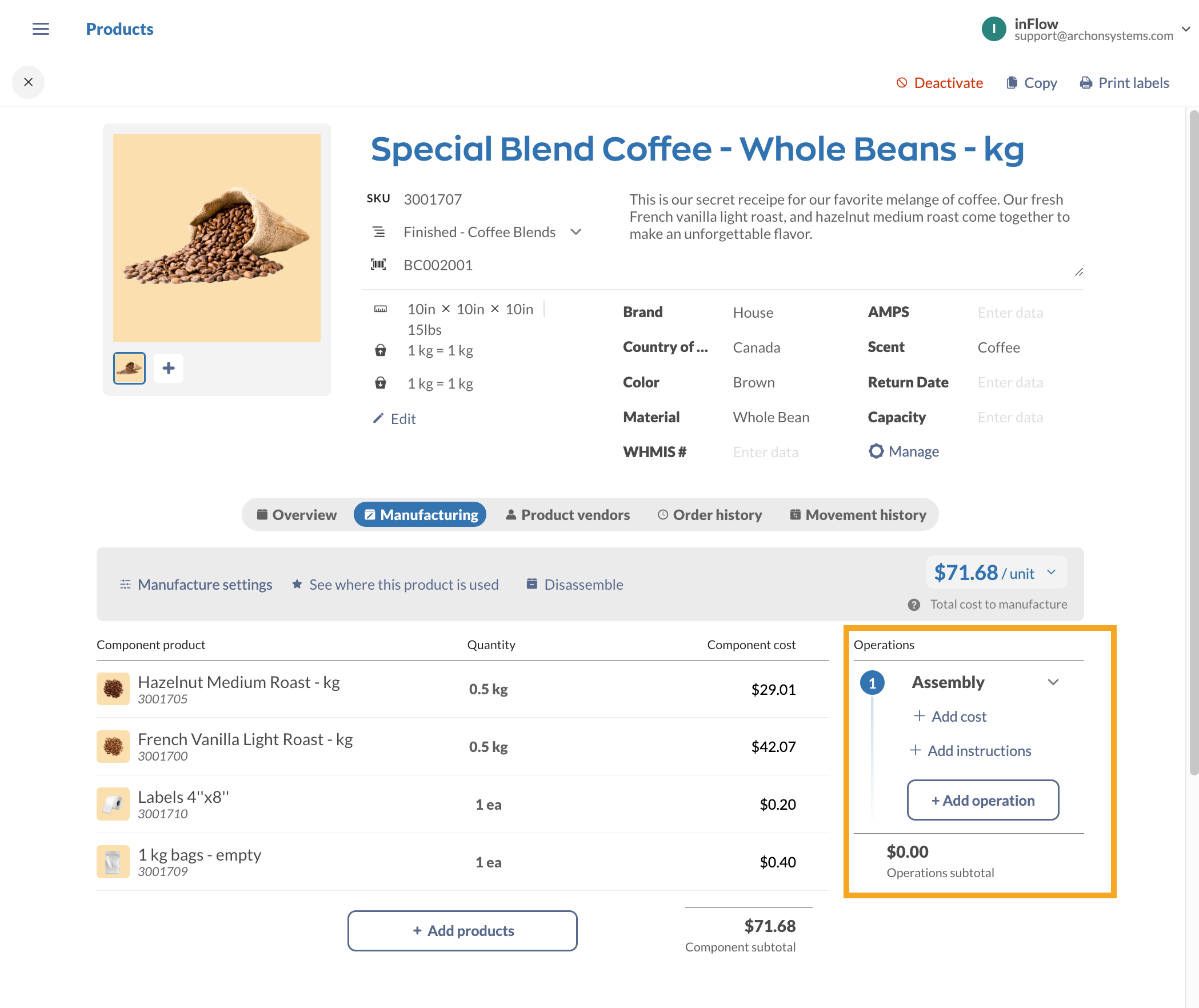
Operation type
Click on the drop-down menu to select the operation type.
The default operation type is Assembly. You can type in new operation types in this field, or you can edit/add operation types in the Inventory settings.
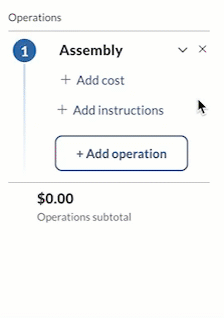
Add cost
This is where you can track the operation cost for this stage of manufacturing and estimate the time it will take. These costs will contribute to the overall manufacturing cost.
Click on Add cost to enter the Labor cost and Estimated duration or Per-unit cost.
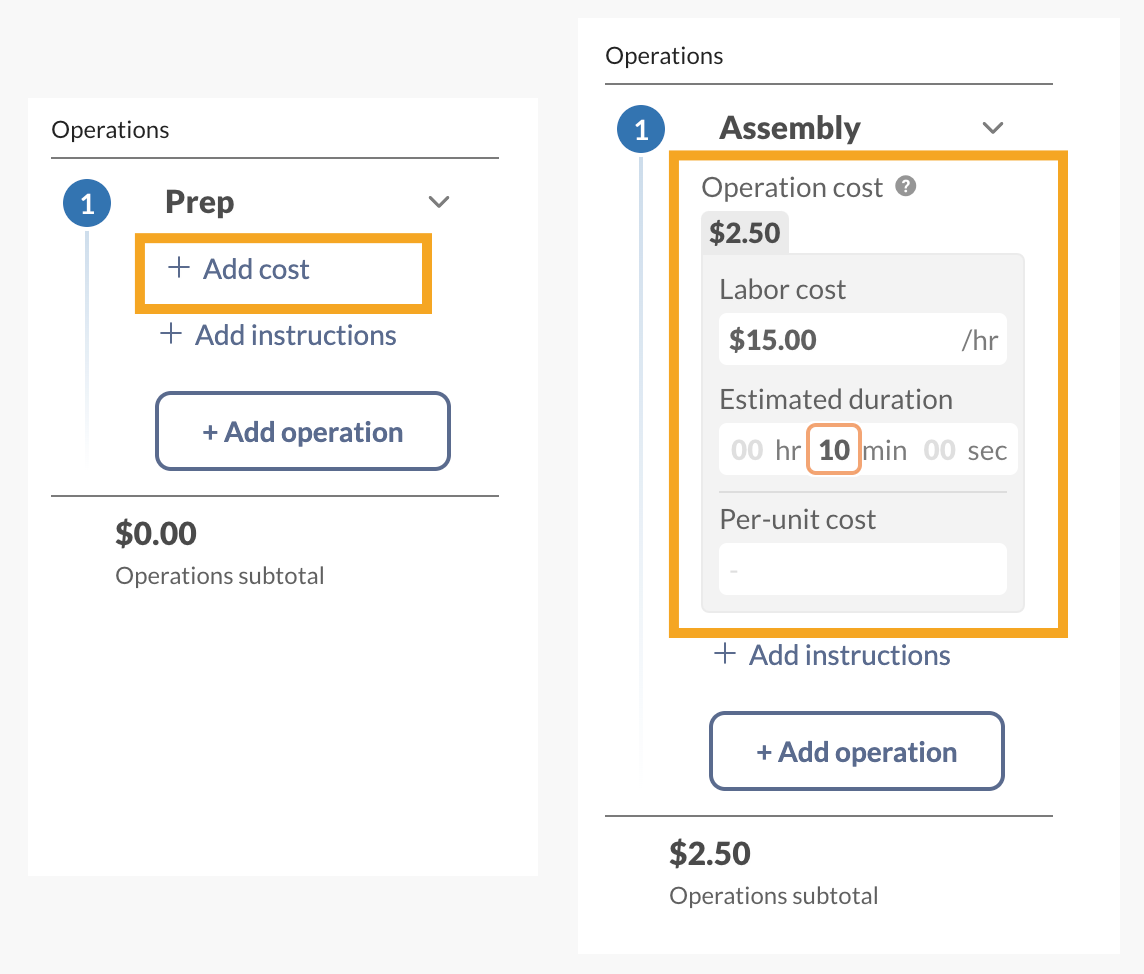
Labor cost | This is to track the hourly rate of the labor used to manufacture for a specific operation. |
Estimated duration | Enter the time in minutes for how long this operation should take. This field holds up to 4 decimal points for precise time tracking. Estimated duration and Labor cost are used to calculate the cost for the specific operation. |
Per-unit cost | This field is used for any fees that are associated with the particular operation. Helpful for tracking costs if the operation is outsourced and you’re charged on a per-unit basis. |
Note: Labor cost, Estimated duration, and Per-unit cost are optional fields.
Add instructions
This field is where you can add written instructions for how to assemble the components in the bill of materials.
Instructions can be simple to read text or include URLs to link out to more complex instructions elsewhere. All URLs must start with either http://
or https://
.
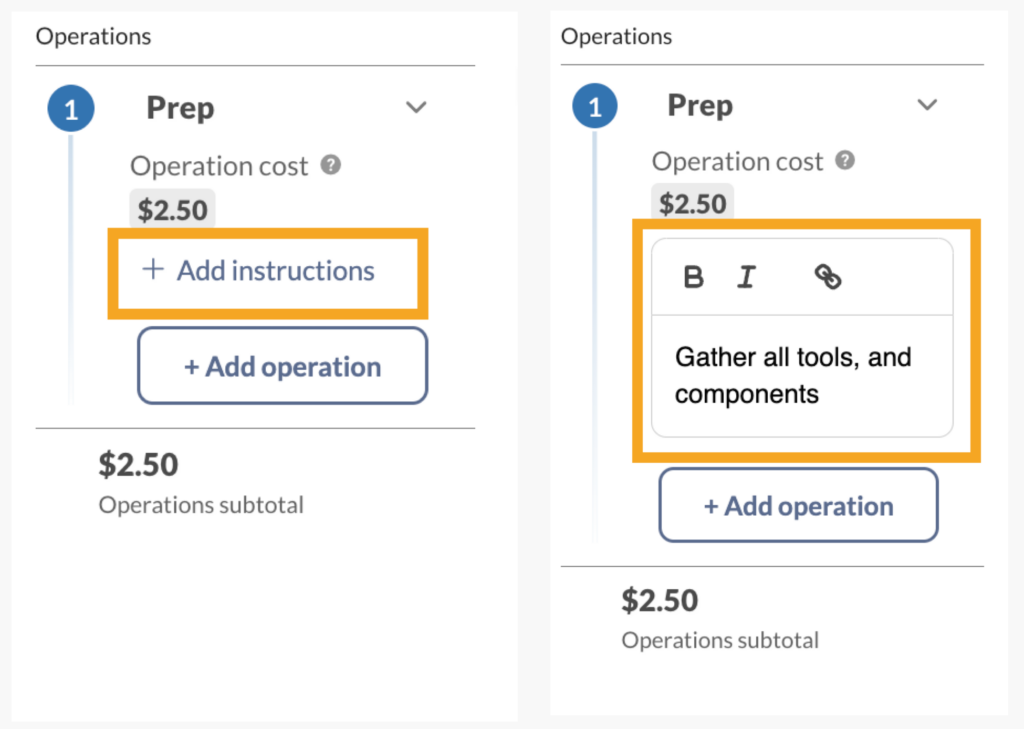
Bill of materials feature video
Manufacturing options
The Manufacturing menu has some helpful tools that can help you stay organized. See below to learn more.
Manufacture settings (Bundles/Kits)
If your company sells individual products as part of a kit or bundle, you can select Auto-assemble from the Manufacture settings to track bundle products. To learn more, take a look at this guide.
See where this product is used
Select See where this product is used to view which bill of materials a product is a part of. This will show a list of finished products, along with the quantities used.
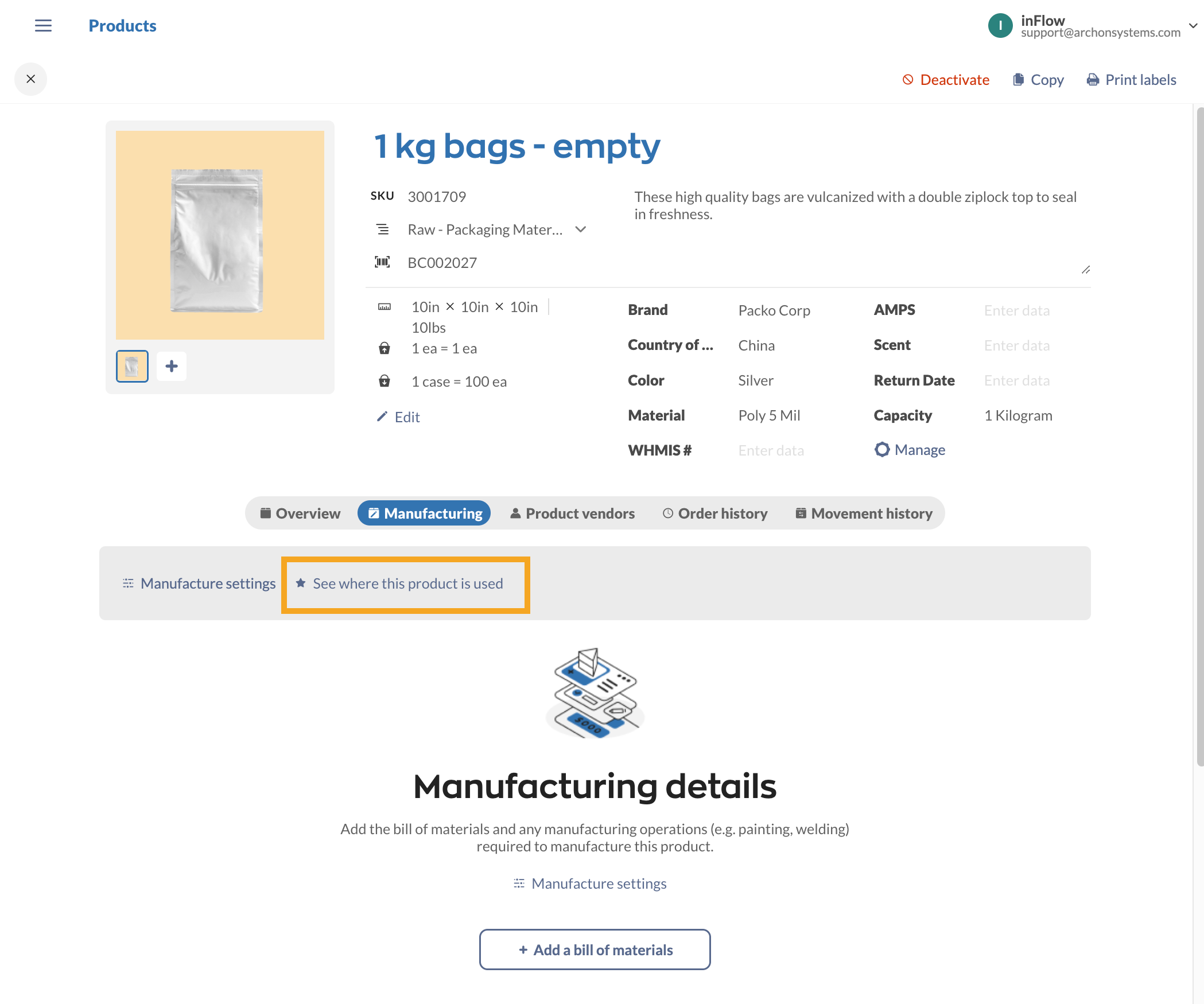
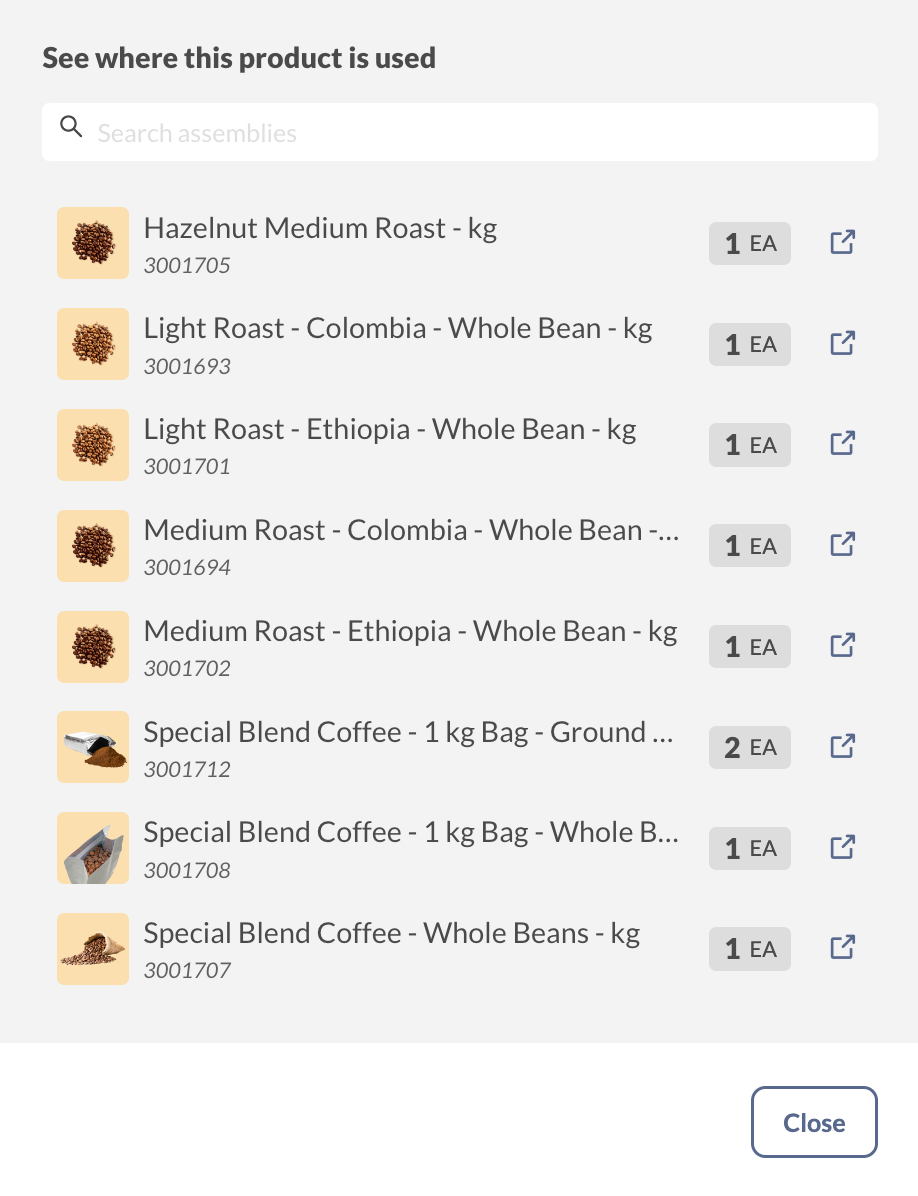
Disassembly
To split a finished product back to the original components, select Disassemble from the Manufacturing tab.
- Select the quantity you want to disassemble.
- Select the location and optional sublocation
- Click Disassemble.
- The window will update to show a new stock adjustment. This will reduce the quantity of the finished product and add quantities based on the bill of materials components.
- You can select View next to the order to look at the stock adjustment in a new tab.
- When finished, click Done.
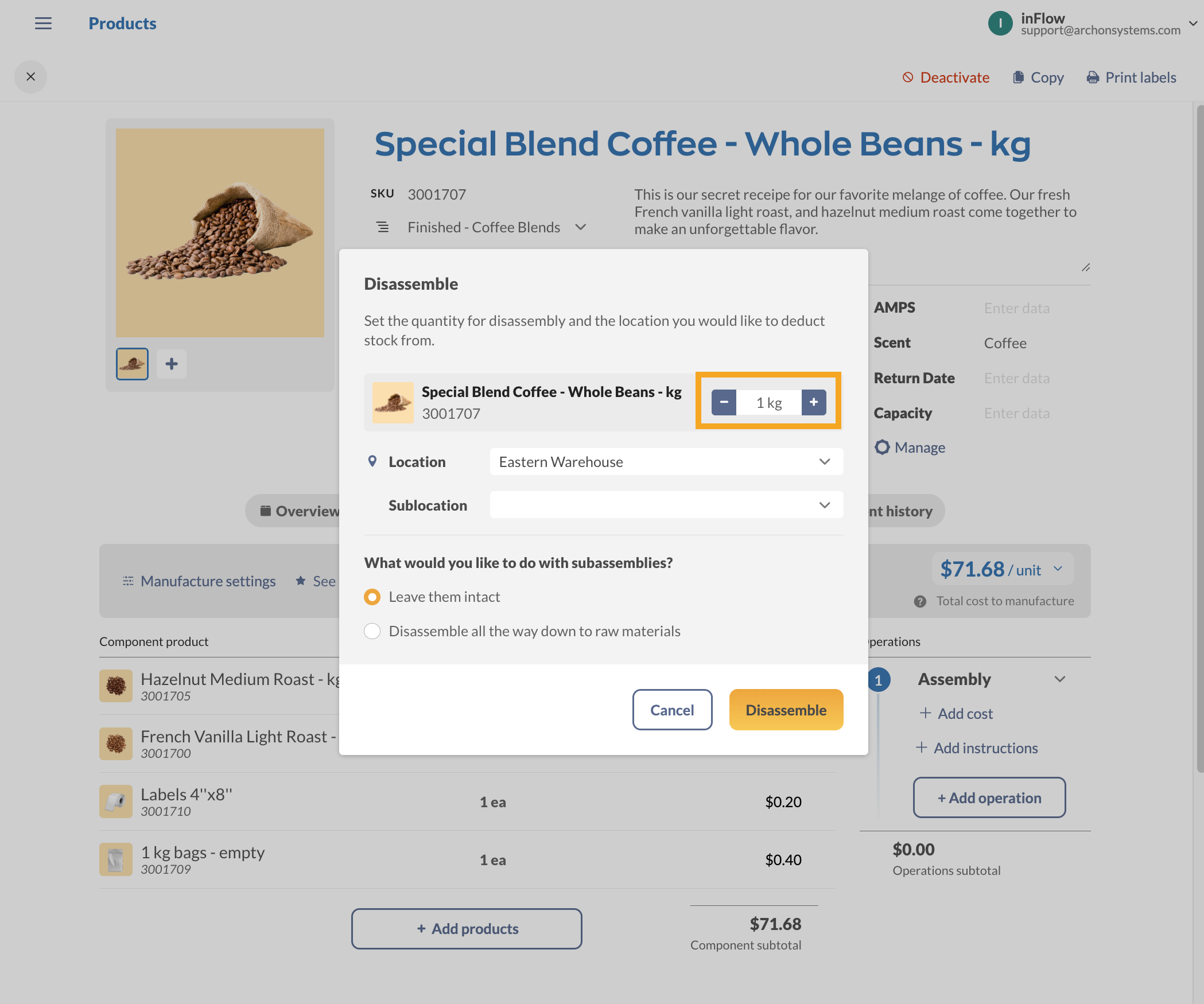
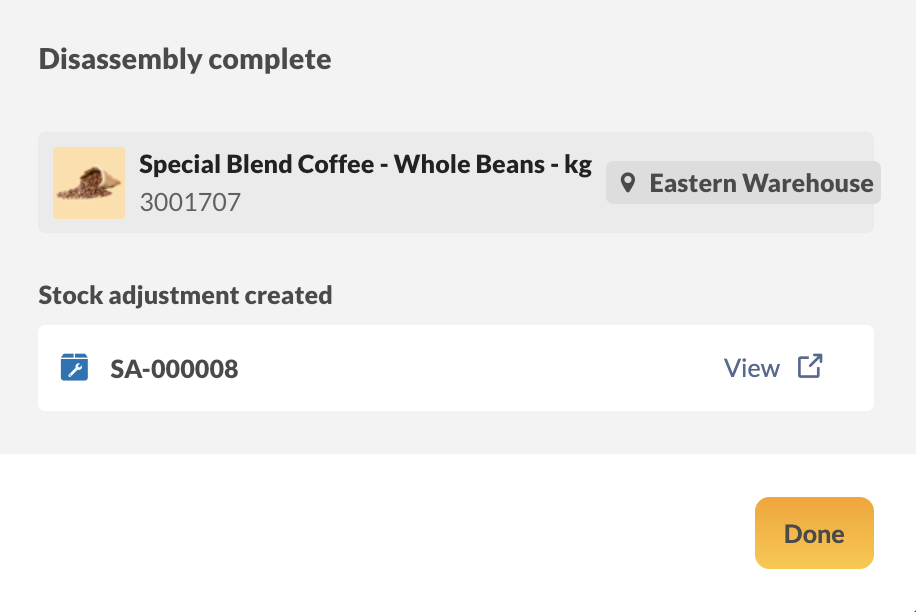
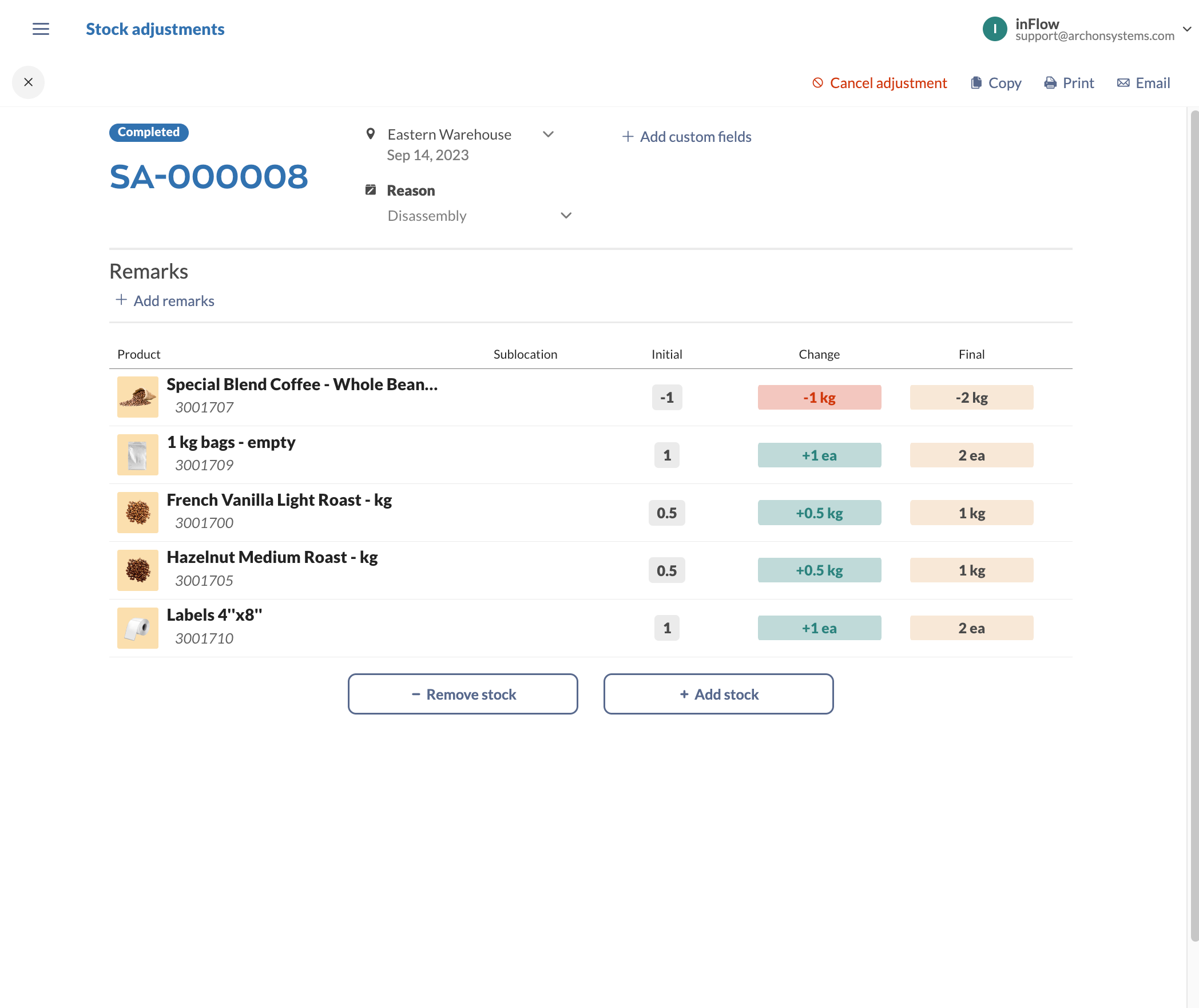
Bundles/Kits
If your company sells individual products as part of a kit or bundle, you can use the Auto-Assemble feature for inFlow to track your kits/bundles. To learn more, take a look at this guide.
0 Comments